Anti-sticking acrylic acid paint for coating and preparation method thereof
An acrylic and anti-adhesive technology, applied in the direction of coating, etc., can solve the problems of restricting wide application, sticky coating film, difficult curing and crosslinking of primer, etc., and achieve good compatibility of general additives, stable polymerization system, easy to control effects
- Summary
- Abstract
- Description
- Claims
- Application Information
AI Technical Summary
Problems solved by technology
Method used
Image
Examples
Embodiment 1
[0024] Prepare raw materials (unit: kg) according to the following components:
[0025]
[0026] Synthetic method: First, mix 2kg sodium dodecylbenzenesulfonate and 1kg sodium alkyl succinate sulfonate with all monomers and stir for 1.5 hours, and the stirring speed is controlled at 80 rpm to obtain pre-emulsion A; 0.4kg over Potassium sulfate and 0.05 kg of tert-butyl hydroperoxide were dissolved in 50 kg of deionized water to form solution B; 0.1 kg of sodium bisulfite and 0.05 kg of sodium formaldehyde sulfoxylate were dissolved in 30 kg of deionized water to form solution C. Add 1 / 6 pre-emulsion A, 1 / 3 solution B and 320kg deionized water into the reactor, control the stirring speed at 160 rpm, raise the temperature to 75°C and react for 30 minutes to obtain the seed emulsion. Start to drop the remaining pre-emulsion A, remaining solution B and solution C, and finish dropping in 3.5 hours, and control the pre-emulsion A to be dropped first, and then the remaining soluti...
Embodiment 2
[0028] Prepare raw materials (unit: kg) according to the following components:
[0029]
[0030]
[0031] Synthetic method: First, mix 0.15 kg sodium dodecylbenzene sulfonate and 0.05 kg sodium alkyl succinate sulfonate with all monomers and stir for 2 hours, and the stirring speed is controlled at 100 rpm to obtain pre-emulsion A; 0.065 Dissolve kg potassium persulfate and 0.006 kg tert-butyl hydroperoxide with 4 kg deionized water to form solution B; dissolve 0.023 kg sodium bisulfite and 0.006 kg formaldehyde sodium sulfoxylate with 2 kg deionized water to form solution C. Add 1 / 6 pre-emulsion A, 1 / 3 solution B and 34kg deionized water into the reactor, control the stirring speed at 175 rpm, raise the temperature to 72°C and react for 60 minutes to obtain the seed emulsion. Start to drop the remaining pre-emulsion A, remaining solution B and solution C, and finish dropping in 3 hours, and control the pre-emulsion A to be dropped first, and then the remaining solution ...
Embodiment 3
[0033] Prepare raw materials (unit: kg) according to the following components:
[0034]
[0035]
[0036] Synthetic method: First, mix 1.2kg sodium dodecylbenzenesulfonate and 0.3kg sodium alkyl succinate sulfonate with all monomers and stir for 1 hour, and the stirring speed is controlled at 60 rpm to obtain pre-emulsion A; 0.25 Dissolve kg potassium persulfate and 0.04 kg tert-butyl hydroperoxide with 30 kg deionized water to form solution B; Add 1 / 6 of the pre-emulsion A, 1 / 3 of the solution B and 150kg of deionized water into the reactor, control the stirring speed at 150 rpm, raise the temperature to 70°C and react for 40 minutes to obtain the seed emulsion. Start to drop the remaining pre-emulsion A, remaining solution B and solution C, and finish dropping in 4 hours, and control the pre-emulsion A to be dropped first, and then the remaining solution B and solution C are dropped at the same time. Keep the reaction at 79°C for 1 hour, lower the temperature to below...
PUM
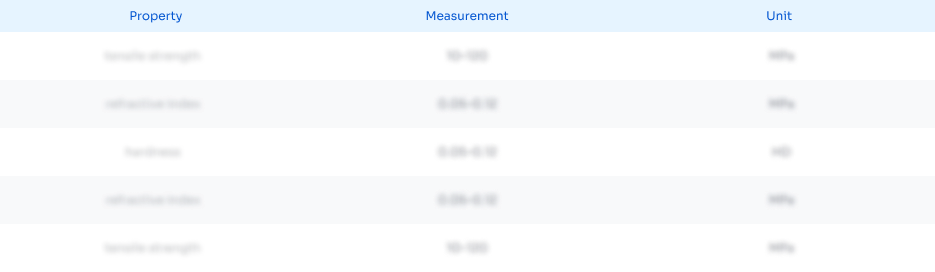
Abstract
Description
Claims
Application Information

- R&D
- Intellectual Property
- Life Sciences
- Materials
- Tech Scout
- Unparalleled Data Quality
- Higher Quality Content
- 60% Fewer Hallucinations
Browse by: Latest US Patents, China's latest patents, Technical Efficacy Thesaurus, Application Domain, Technology Topic, Popular Technical Reports.
© 2025 PatSnap. All rights reserved.Legal|Privacy policy|Modern Slavery Act Transparency Statement|Sitemap|About US| Contact US: help@patsnap.com