Piquancy slow-release noodles and processing method thereof
A processing method and slow-release technology, which are applied in the field of spicy slow-release noodles and their processing, can solve problems such as limited application and spicy taste, and achieve the effects of promoting deep processing, being difficult to release, and reducing sensory spiciness.
- Summary
- Abstract
- Description
- Claims
- Application Information
AI Technical Summary
Problems solved by technology
Method used
Image
Examples
Embodiment 1
[0040] Embodiment 1: get 100kg flour, salt 1kg, sodium carbonate 0.15kg, sodium alginate 0.1kg, water 18kg is evenly stirred to form upper and lower two-layer sheet raw material; Get 100kg flour, capsicum oleoresin 0.005 kg, salt 1kg, sodium carbonate 0.15kg, 0.1kg of sodium alginate, and 18kg of water are uniformly stirred to form the raw material of the middle layer sheet;
[0041] Press the raw materials of the upper, middle and lower layers respectively to a thickness of 5 mm to form the upper, middle and lower layers; calender the upper, middle and lower layers to form a composite dough, so that the thickness of the composite dough is 5 mm; Place the composite dough sheet at room temperature 30°C for 10 minutes; press the composite dough sheet into a thickness of about 0.06mm through three times of calendering, and cut it into noodles with a width of 0.8mm and a length of 1.2m; dry the noodles with hot air , so that its moisture content is not higher than 13.5%; the hot-a...
Embodiment 2
[0042] Embodiment 2: get 100kg of flour, 1.5kg of salt, 0.175kg of sodium carbonate, 0.125kg of sodium alginate, and 20kg of water are evenly stirred to form upper and lower two-layer sheet raw materials; get 100kg of flour, 0.013 kg of capsicum oleoresin, 1.5kg of salt, 0.175kg of sodium carbonate, 0.125kg of sodium alginate, and 20kg of water are evenly stirred to form the raw material of the middle layer sheet;
[0043] Press the raw materials of the upper, middle and lower layers respectively to a thickness of 7 mm to form the upper, middle and lower layers; calender the upper, middle and lower layers to form a composite dough, so that the thickness of the composite dough is 7 mm; Place the composite dough sheet at room temperature 35°C for 20 minutes; press the composite dough sheet into a dough sheet with a thickness of about 1 mm through 5 times of calendering, and cut it into noodles with a width of 5 mm and a length of 1.6 m; dry the noodles with hot air to make Its m...
Embodiment 3
[0044]Embodiment 3: get 100kg of flour, 2kg of salt, 0.2kg of sodium carbonate, 0.15kg of sodium alginate, and 22kg of water are evenly stirred to form the upper and lower two-layer sheet raw materials; get 100kg of flour, 0.02 kg of ethanol extract of capsicum, 2kg of salt, 0.2kg of sodium carbonate, 0.15kg of sodium alginate, and 22kg of water are evenly stirred to form the raw material of the middle layer; the raw materials of the upper, middle and lower layers are respectively pressed to a thickness of 10mm to form the upper, middle and lower layers; , The lower layer sheet is calendered and combined into a composite dough sheet, so that the thickness of the composite dough sheet is 10mm; the composite dough sheet is placed at a room temperature of 40°C for 30 minutes; after 7 times of calendering, the composite dough sheet is pressed to a thickness of about 1.4mm Noodles, cut into 10mm wide and 2m long noodles; dry the noodles with hot air so that the moisture content is n...
PUM
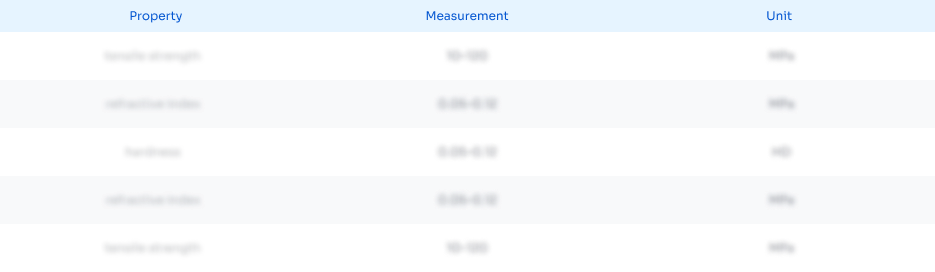
Abstract
Description
Claims
Application Information

- Generate Ideas
- Intellectual Property
- Life Sciences
- Materials
- Tech Scout
- Unparalleled Data Quality
- Higher Quality Content
- 60% Fewer Hallucinations
Browse by: Latest US Patents, China's latest patents, Technical Efficacy Thesaurus, Application Domain, Technology Topic, Popular Technical Reports.
© 2025 PatSnap. All rights reserved.Legal|Privacy policy|Modern Slavery Act Transparency Statement|Sitemap|About US| Contact US: help@patsnap.com