Multi-level impulse bagasse drying system
A drying system, pulsed technology, applied in the direction of drying solid materials, drying gas arrangement, heating to dry solid materials, etc., to achieve the effect of offsetting pressure loss, high stability and better energy saving effect
- Summary
- Abstract
- Description
- Claims
- Application Information
AI Technical Summary
Problems solved by technology
Method used
Image
Examples
Embodiment 1
[0034] This multi-stage pulse type bagasse drying system uses boiler flue gas as the drying source, adopts the original equipment including the original boiler flue 1, dust collector 19, induced draft fan 20 and chimney 21, and closes the bypass bagasse drying system of the original flue 8 The air gate B7 is set between the boiler flue gas inlet and outlet. The high-temperature boiler flue gas flows from the boiler flue 1 to the boiler flue gas inlet of the bypass bagasse drying system through the original flue 8, and passes through the opened bypass bagasse drying system. Boiler flue gas inlet damper A6, the first spark cyclone separator entering into spark separator 9 and the second cluster type spark cyclone separator consisting of 16 small spark cyclones separate and purify the boiler flue gas Boiler flue gas with a temperature of 290°C and no sparks.
[0035] Under the inventor's Chinese patent ZL 200420048043.9 drum-type bagasse feeder 4, the storage capacity of the baga...
Embodiment 2
[0039] This multi-stage pulse type bagasse drying system uses boiler flue gas as the drying source, adopts the original equipment including the original boiler flue 1, dust collector 19, induced draft fan 20 and chimney 21, and closes the bypass bagasse drying system of the original flue 8 The air gate B7 is set between the boiler flue gas inlet and outlet. The high-temperature boiler flue gas flows from the boiler flue 1 to the boiler flue gas inlet of the bypass bagasse drying system through the original flue 8, and passes through the opened bypass bagasse drying system. The boiler flue gas inlet damper A6 enters the cluster type spark cyclone separator composed of 20 small spark cyclone separators 9 to separate the boiler flue gas to obtain purified boiler flue gas with a temperature of 278°C and no sparks.
[0040] Under the inventor's Chinese patent ZL 200420048043.9 drum-type bagasse feeder 4, the storage capacity of the bagasse barrel 3, the automatic instrument control ...
PUM
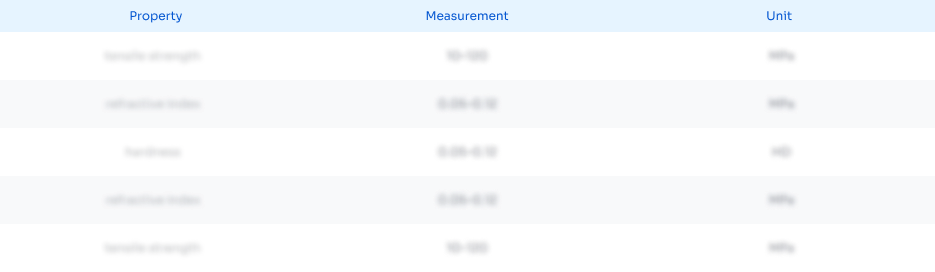
Abstract
Description
Claims
Application Information

- Generate Ideas
- Intellectual Property
- Life Sciences
- Materials
- Tech Scout
- Unparalleled Data Quality
- Higher Quality Content
- 60% Fewer Hallucinations
Browse by: Latest US Patents, China's latest patents, Technical Efficacy Thesaurus, Application Domain, Technology Topic, Popular Technical Reports.
© 2025 PatSnap. All rights reserved.Legal|Privacy policy|Modern Slavery Act Transparency Statement|Sitemap|About US| Contact US: help@patsnap.com