Recycling method of output coal gas in iron making technology
A gas and process technology, applied in the field of two-stage ironmaking process, can solve the problems of decreased gas production, lower fuel ratio, large fluctuations, etc., achieve the effect of abundant gas, stable factory pressure, and reduced energy consumption
- Summary
- Abstract
- Description
- Claims
- Application Information
AI Technical Summary
Problems solved by technology
Method used
Image
Examples
Embodiment 1
[0042] Under the conditions of high smelting rate (180t / h) and low fuel (700kg / tHM) ratio, the amount of gas generated is 240000Nm 3 / h or so, pre-reduction needs gas 270000-280000Nm 3 / h, the output gas line needs to be opened, and the amount of cold gas added is 60000Nm 3 / h, the output gas circulation volume is less than the cold gas addition amount, open the cold gas line cut-off valve, turn on the cold gas pressurizer, the cold gas flow rate is 50000Nm 3 / h, the total cold gas volume is the output gas circulation volume plus the cold gas volume, which is about 100000Nm 3 / h, these cold gas in addition to meet the cold gas addition, the extra 40000Nm 3 / h returns through the bypass valve. Adjust the amount of cold gas added by adjusting the opening of the bypass valve to ensure that the overall gas temperature after mixing is around 850°C to meet the temperature requirements of the reduced gas in the pre-reduction reactor.
Embodiment 2
[0044] When the smelting rate is low (120t / h) and the fuel ratio is low (700kg / tHM), the amount of gas generated is 160000Nm 3 / h or so, pre-reduction requires gas 183000Nm 3 / h, open the output gas circulation line, the amount of cold gas added is about 40000Nm 3 / h, the amount of output gas circulation is greater than the amount of cold gas added, in order to save power consumption, turn off the cold gas compressor, close the cut-off valve of the cold gas line, the total amount of cold gas is provided by the output gas cycle, in addition to meeting the cold gas addition, the redundant The cold gas is discharged from the excess gas through the bypass valve. In this mode, the amount of cold gas added is still adjusted by adjusting the opening of the bypass valve to ensure that the temperature of the gas after mixing is at 850°C.
Embodiment 3
[0046] When the fuel ratio is greater than 850kg / tHM, the final reduction gas volume is greater than or equal to the pre-reduction gas consumption, and the final reduction gas production meets the pre-reduction gas demand, and there is no need to open the output gas circulation line. Therefore, close the cut-off valve of the output gas circulation line, open the cold gas line cut-off valve, and start the cold gas pressurizer.
[0047] To sum up, with the improvement of the fuel quality and operation of the final reduction reactor, the fuel ratio and coke ratio have dropped significantly, and the amount of gas produced by the final reduction reactor cannot meet the amount of gas required for the reduction of the pre-reduction reactor. will become more prominent. In order to solve the problem of gas shortage, the present invention returns part of the output gas and mixes it with generated gas after treatment, which can meet the gas demand of the pre-reduction reactor and solve t...
PUM
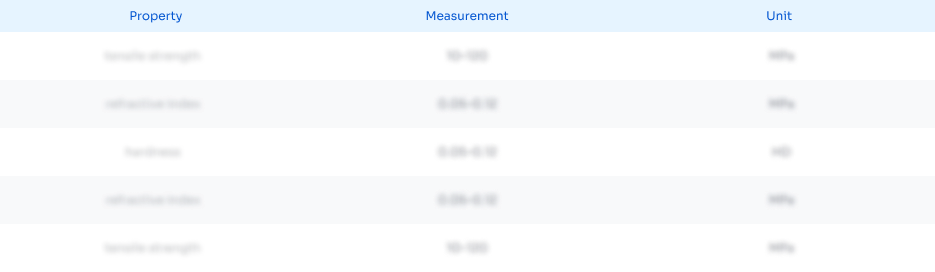
Abstract
Description
Claims
Application Information

- Generate Ideas
- Intellectual Property
- Life Sciences
- Materials
- Tech Scout
- Unparalleled Data Quality
- Higher Quality Content
- 60% Fewer Hallucinations
Browse by: Latest US Patents, China's latest patents, Technical Efficacy Thesaurus, Application Domain, Technology Topic, Popular Technical Reports.
© 2025 PatSnap. All rights reserved.Legal|Privacy policy|Modern Slavery Act Transparency Statement|Sitemap|About US| Contact US: help@patsnap.com