Process for carrying out simulation copperplate etching printing on surface of paper product
A process method and paper technology, applied in printing, printing device, temperature recording method, etc., can solve the problems of inability to achieve copper plate etching, no metal feeling and layering.
- Summary
- Abstract
- Description
- Claims
- Application Information
AI Technical Summary
Problems solved by technology
Method used
Examples
Embodiment 1
[0007] Print spot colors on paper, where the L value is 34, the A value is 8, and the B value is 6. Place the anodized aluminum hot stamping paper on the printing surface of the above paper product, and hot stamp the printing surface of the paper product by means of the hot stamping plate installed on the hot stamping machine. The L value of the above-mentioned anodized aluminum hot stamping paper is 40, the A value is 16, the B value is 8, and the hot stamping temperature is 100°C.
Embodiment 2
[0009] Print spot colors on paper, where the L value is 40, the A value is 15, and the B value is 12. Place the anodized aluminum hot stamping paper on the printing surface of the above paper product, and hot stamp the printing surface of the paper product by means of the hot stamping plate installed on the hot stamping machine. The L value of the above-mentioned anodized aluminum hot stamping paper is 46, the A value is 22, the B value is 14, and the hot stamping temperature is 120°C.
Embodiment 3
[0011] Print spot colors on paper, where the L value is 47, the A value is 22, and the B value is 19. Place the anodized aluminum hot stamping paper on the printing surface of the above paper product, and hot stamp the printing surface of the paper product by means of the hot stamping plate installed on the hot stamping machine. The L value of the above-mentioned anodized aluminum hot stamping paper is 52, the A value is 29, the B value is 21, and the hot stamping temperature is 140°C.
PUM
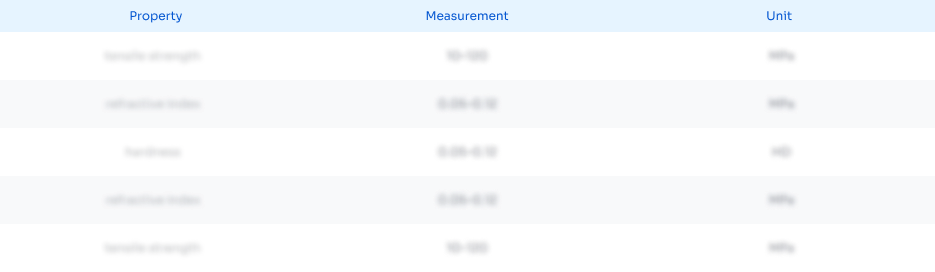
Abstract
Description
Claims
Application Information

- R&D Engineer
- R&D Manager
- IP Professional
- Industry Leading Data Capabilities
- Powerful AI technology
- Patent DNA Extraction
Browse by: Latest US Patents, China's latest patents, Technical Efficacy Thesaurus, Application Domain, Technology Topic, Popular Technical Reports.
© 2024 PatSnap. All rights reserved.Legal|Privacy policy|Modern Slavery Act Transparency Statement|Sitemap|About US| Contact US: help@patsnap.com