Electric control cabinet material bridge mould with primary back pressure workstation
An electrical control cabinet, the first station technology, applied in the direction of forming tools, manufacturing tools, metal processing equipment, etc., can solve problems such as increasing production costs, process redundancy, etc., to overcome warping deformation, save processes, and reduce production. cost effect
- Summary
- Abstract
- Description
- Claims
- Application Information
AI Technical Summary
Problems solved by technology
Method used
Image
Examples
Embodiment Construction
[0025] Hereinafter, the present invention will be further described with reference to the accompanying drawings.
[0026] like figure 1 As shown, an electrical control cabinet material bridge mold with a primary back pressure station includes an upper mold and a lower mold facing the upper mold, and the electrical control cabinet material bridge mold with a primary back pressure station is provided with a A first station for forming and a second station for back pressure, the first station and the second station are arranged in sequence.
[0027] like figure 2 As shown in the above-mentioned electrical control cabinet material bridge mold with a primary back pressure station, the first station includes a first upper punching block and a first lower punching block facing the first upper punching block. The first upper punching block is fixedly connected to the upper die, and the first lower punching block is fixedly connected to the lower die. The first upper punching block...
PUM
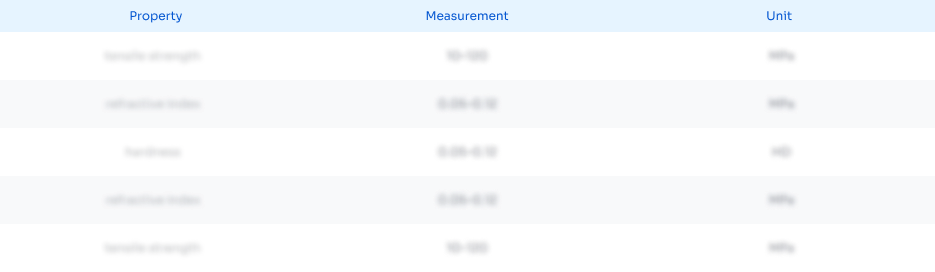
Abstract
Description
Claims
Application Information

- Generate Ideas
- Intellectual Property
- Life Sciences
- Materials
- Tech Scout
- Unparalleled Data Quality
- Higher Quality Content
- 60% Fewer Hallucinations
Browse by: Latest US Patents, China's latest patents, Technical Efficacy Thesaurus, Application Domain, Technology Topic, Popular Technical Reports.
© 2025 PatSnap. All rights reserved.Legal|Privacy policy|Modern Slavery Act Transparency Statement|Sitemap|About US| Contact US: help@patsnap.com