Method for manufacturing plastic bonded permanent magnet rotor with buffering layer
A technology of bonded magnets and permanent magnet rotors, which is applied in the manufacture of stator/rotor bodies, etc.
- Summary
- Abstract
- Description
- Claims
- Application Information
AI Technical Summary
Problems solved by technology
Method used
Image
Examples
Embodiment 1
[0028] The bonded magnet 1 is made of nylon 12 bonded strontium ferrite, and the buffer layer 2 is made of nylon 12; the cross section of the buffer layer 2 is circular;
[0029] Its preparation method is:
[0030] Step 1: Put the metal shaft 3 in the mold, the mold temperature is 80°C, dry the nylon 12 at 80°C for at least 4 hours, and then inject the buffer layer 2 through the injection molding machine to become a semi-finished product, the injection temperature is 240°C, and the injection rate is 80mm / s, open the mold after cooling for 10 seconds and take out the semi-finished product;
[0031] Step 2: Place the above-mentioned semi-finished product in the permanent magnet rotor mold, the mold temperature is 80°C, dry the above-mentioned nylon 12 bonded strontium ferrite at 80°C for at least 4 hours, and then inject the bonded magnet part through the injection molding machine, the injection temperature is 280°C ℃, the injection rate is 60mm / s, after cooling for 10 seconds...
Embodiment 2
[0034] The bonded magnet 1 is made of nylon 6 bonded strontium ferrite, and the buffer layer 2 is made of nylon 6; the cross section of the buffer layer 2 is circular;
[0035] Its preparation method is:
[0036] Step 1: Put the metal shaft 3 in the mold, the mold temperature is 80°C, dry nylon 6 at 80°C for at least 4 hours, and then inject the buffer layer 2 through the injection molding machine to become a semi-finished product, the injection temperature is 240°C, and the injection rate is 80mm / s, open the mold after cooling for 10 seconds and take out the semi-finished product;
[0037] Step 2: Place the above-mentioned semi-finished product in the permanent magnet rotor mold, the mold temperature is 80°C, dry the above-mentioned nylon 6 bonded strontium ferrite at 80°C for at least 4 hours, and then inject the bonded magnet part through the injection molding machine, the injection temperature is 285°C ℃, the injection rate is 60mm / s, after cooling for 10 seconds, the mo...
Embodiment 3
[0040] The bonded magnet 1 is made of polyphenylene sulfide bonded strontium ferrite, and the buffer layer 2 is made of polyphenylene sulfide; the cross section of the buffer layer 2 is circular;
[0041] Its preparation method is:
[0042] Step 1: Put the metal shaft in the mold, the mold temperature is 120°C, dry the polyphenylene sulfide at 100°C for at least 4 hours, and then inject the buffer layer 2 through the injection molding machine to become a semi-finished product, the injection temperature is 320°C, and the injection speed is 80mm / s, open the mold after cooling for 10 seconds and take out the semi-finished product;
[0043] Step 2: Place the above-mentioned semi-finished product in the permanent magnet rotor mold, the mold temperature is 120°C, dry the above-mentioned polyphenylene sulfide bonded strontium ferrite at 100°C for at least 4 hours, and then inject the bonded magnet part through the injection molding machine, inject The temperature is 320°C, the inje...
PUM
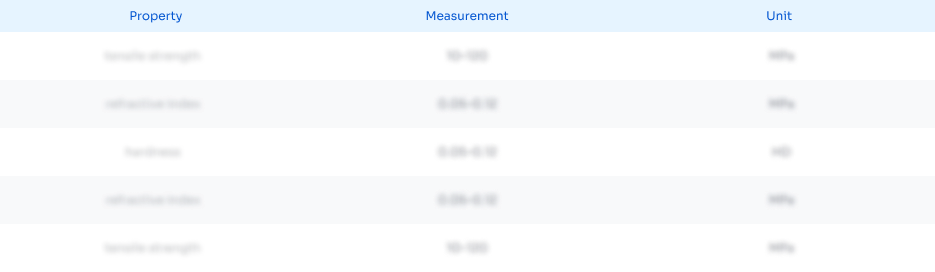
Abstract
Description
Claims
Application Information

- R&D Engineer
- R&D Manager
- IP Professional
- Industry Leading Data Capabilities
- Powerful AI technology
- Patent DNA Extraction
Browse by: Latest US Patents, China's latest patents, Technical Efficacy Thesaurus, Application Domain, Technology Topic, Popular Technical Reports.
© 2024 PatSnap. All rights reserved.Legal|Privacy policy|Modern Slavery Act Transparency Statement|Sitemap|About US| Contact US: help@patsnap.com