Three-axis-system composite spinning device and spinning method for tow-apt-to-fall staple
A composite spinning and staple fiber technology, which is applied in the direction of continuous winding spinning machines, spinning machines, textiles and papermaking, etc., can solve the problems that do not involve kapok fiber triaxial composite spinning devices and methods, and achieve Excellent quality, strong controllability, convenient and innovative effects
- Summary
- Abstract
- Description
- Claims
- Application Information
AI Technical Summary
Problems solved by technology
Method used
Image
Examples
Embodiment 1
[0021] like figure 1 As shown, it is a structural schematic diagram of the first three-axis composite spinning device for easy-to-dump short fibers. The three-axis composite spinning device includes a ring spinning frame with a front roller 7, and the front roller Near the feeding jaw of 7, be provided with easily shedding short fiber sliver locator 4, cotton sliver locator 5 and long tow adjustable tension wheel 6. The relative positions between the easy-to-dandruff short fiber sliver positioner 4, the cotton sliver sliver positioner 5, and the adjustable tension wheel 6 for filament bundles can be adjusted. It is located between the sliver sliver positioner 5 and the adjustable tension wheel 6 of the filament bundle.
Embodiment 2
[0023] like figure 2 As shown, it is a schematic structural diagram of the second three-axis composite spinning device for easy-to-dump short fibers. The three-axis composite spinning device includes a ring spinning frame with a front roller 7, and the front roller Near the feeding jaw of 7, be provided with easily shedding short fiber sliver locator 4, cotton sliver locator 5 and long tow adjustable tension wheel 6. The relative positions between the easy-to-shred short fiber sliver locator 4, the cotton sliver locator 5 and the adjustable tension wheel 6 of the filament bundle can be adjusted, and the adjustable tension wheel 6 of the filament bundle is located at the easy Between the crumb short fiber sliver locator 4 and the cotton sliver sliver locator 5.
Embodiment 3
[0025] Using the three-axis composite spinning device of the easy-to-break short fiber described in Example 1, the kapok roving sliver and the cotton roving sliver are fed into the rear roller 10 of the ring spinning frame at a certain distance, and formed after drafting Straighten the parallel easy-to-shred short fiber strands (i.e. kapok strands) 1 and cotton strands 2; use the easy-to-shred short-fiber strands 1 and cotton strands 2 respectively with the easy-to-shred short-fiber locator 4 After being positioned with the sliver sliver positioner 5, it is fed into the jaws of the front roller 7, and the filament bundle (polyester textured yarn) 3 is directly fed into the jaws of the front roller 7 through the filament bundle adjustable tension wheel 6 to form a three-axis system Feeding: After the short fiber strands 1, cotton strands 2 and filament bundles 3 are output from the front roller 7 nip, the position of the staple strands 1 and the tension of the filament strands 3...
PUM
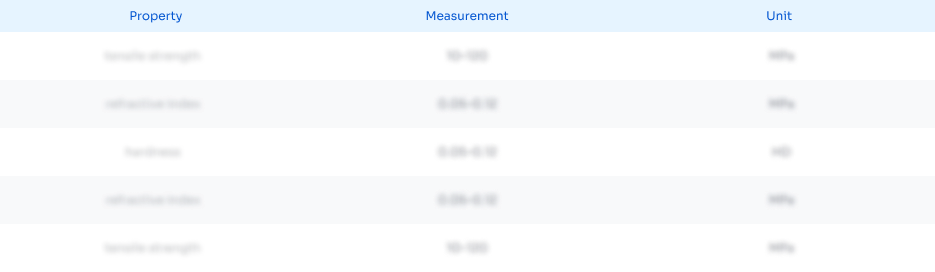
Abstract
Description
Claims
Application Information

- Generate Ideas
- Intellectual Property
- Life Sciences
- Materials
- Tech Scout
- Unparalleled Data Quality
- Higher Quality Content
- 60% Fewer Hallucinations
Browse by: Latest US Patents, China's latest patents, Technical Efficacy Thesaurus, Application Domain, Technology Topic, Popular Technical Reports.
© 2025 PatSnap. All rights reserved.Legal|Privacy policy|Modern Slavery Act Transparency Statement|Sitemap|About US| Contact US: help@patsnap.com