Optimized stamping process for diaphragm spring with DST (direct solution treatment) structure
A stamping and leaf spring technology, applied in the field of optimized stamping process of DST structure diaphragm spring, can solve the problems of low product dimensional accuracy, low production efficiency, and many technological processes, and achieves elimination of errors, improvement of fatigue life, extraction of The effect of efficiency
- Summary
- Abstract
- Description
- Claims
- Application Information
AI Technical Summary
Problems solved by technology
Method used
Image
Examples
Embodiment Construction
[0021] refer to figure 1 , the DST structure diaphragm spring blanking, punching hole, and window mold of the present invention include an upper template 1, a screw 2, an upper backing plate 3, a punch fixing plate 4, a die holding plate 5, a die 6, Window punch 7, upper unloading plate 8, lower unloading plate 9, middle hole punch 10, unloading screw 11, convex and concave die 12, lower backing plate 13, lower template 14, rubber 15, stopper pin 16, guide post 17 , guide sleeve 18 and cylindrical pin 19, window punch 7 and center hole punch 10 are fixed on the punch fixing plate 4, the die 6 is connected and fixed on the punch fixing plate 4 by screws 2 and the die holding plate 5 is held tightly , in order to prevent the sheets from being stuck, an upper unloading plate 8, a lower unloading plate 9 and an unloading screw 11 are also provided. The upper unloading plate 8 is fixed on the punch fixing plate 4 through the unloading screw 11, and the lower unloading plate The pl...
PUM
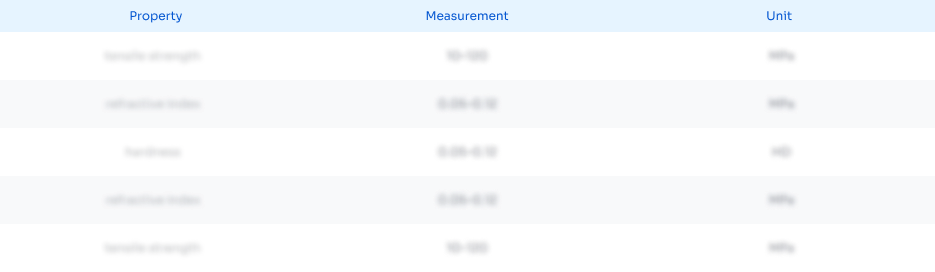
Abstract
Description
Claims
Application Information

- R&D Engineer
- R&D Manager
- IP Professional
- Industry Leading Data Capabilities
- Powerful AI technology
- Patent DNA Extraction
Browse by: Latest US Patents, China's latest patents, Technical Efficacy Thesaurus, Application Domain, Technology Topic, Popular Technical Reports.
© 2024 PatSnap. All rights reserved.Legal|Privacy policy|Modern Slavery Act Transparency Statement|Sitemap|About US| Contact US: help@patsnap.com