A Method for Evaluating the Comprehensive Alkali Removal and Desulfurization Ability of Blast Furnace Slag
A blast furnace slag and capacity technology, applied in the field of metallurgical physical and chemical testing, can solve the problems of unstudied slag alkali discharge, desulfurization thermodynamic parameters, inaccurate thermodynamic conditions, poor applicability of research results, etc., and achieve the effect of simple method and good reproducibility
- Summary
- Abstract
- Description
- Claims
- Application Information
AI Technical Summary
Problems solved by technology
Method used
Image
Examples
Embodiment 1
[0057] Example 1: Take CaO and SiO that have been calcined at 1100°C for 12 hours 2 、Al 2 o 3 , MgO, TiO 2 Chemical reagents are mixed according to the mass ratio of 32.3%, 34.78%, 15.44%, 16.8%, and 0.68%, and then put into a graphite crucible, mixed and melted at 1500°C, fully stirred, taken out, cooled, and crushed to make a slag sample for later use. Weigh 60 grams of potassium carbonate and put it into a corundum crucible, place the crucible at a temperature of 1350°C in a high-temperature furnace; take another 40 grams of slag prepared in the first step and place it in a platinum crucible, which is located at the porous height of the corundum crucible Aluminum refractory bricks, so that the corundum crucible is in the constant temperature zone of the high temperature furnace. When the furnace temperature rises to 1000°C, Ar is introduced from the bottom of the corundum tube to remove the air in the corundum tube. When the furnace temperature rises to 1500°C, the purif...
Embodiment 2
[0058] Example 2: Take CaO and SiO that have been calcined at 1100°C for 12 hours 2 、Al 2 o 3 , MgO, TiO 2 The chemical reagents are mixed according to the mass ratio of 42.3%, 34.33%, 15.44%, 7.25%, and 0.68%, and then put into a graphite crucible, mixed and melted at 1500°C, fully stirred, taken out, cooled, and crushed to make a slag sample for later use. Weigh 60 grams of potassium carbonate and put it into a corundum crucible, place the crucible at a temperature of 1350°C in a high-temperature furnace; take another 40 grams of slag prepared in the first step and place it in a platinum crucible, which is located at the porous height of the corundum crucible Aluminum refractory bricks, so that the corundum crucible is in the constant temperature zone of the high temperature furnace. When the furnace temperature rises to 1000°C, Ar is introduced from the bottom of the corundum tube to remove the air in the corundum tube. When the furnace temperature rises to 1500°C, the p...
Embodiment 3
[0059] Example 3: Take CaO and SiO that have been calcined at 1100°C for 12 hours 2 、Al 2 o 3 , MgO, TiO 2 Chemical reagents are mixed according to the mass ratio of 38.20%, 34.86%, 15.44%, 10.82%, and 0.68%, and then put into a graphite crucible, mixed and melted at 1500°C, fully stirred, taken out, cooled, and crushed to make a slag sample for later use. Weigh 60 grams of potassium carbonate and put it into a corundum crucible, place the crucible at a temperature of 1350°C in a high-temperature furnace; take another 40 grams of slag prepared in the first step and place it in a platinum crucible, which is located at the porous height of the corundum crucible Aluminum refractory bricks, so that the corundum crucible is in the constant temperature zone of the high temperature furnace. When the furnace temperature rises to 1000°C, Ar is introduced from the bottom of the corundum tube to remove the air in the corundum tube. When the furnace temperature rises to 1410°C, the pur...
PUM
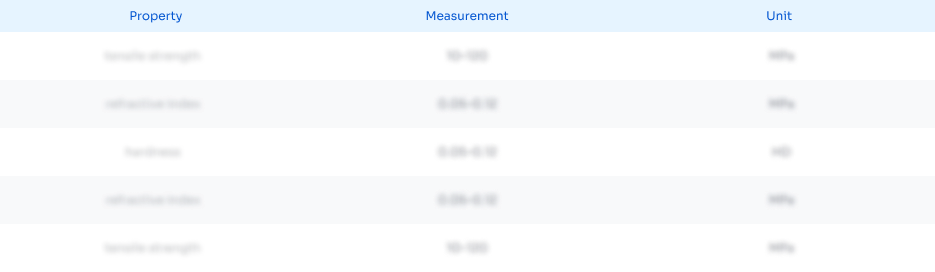
Abstract
Description
Claims
Application Information

- R&D
- Intellectual Property
- Life Sciences
- Materials
- Tech Scout
- Unparalleled Data Quality
- Higher Quality Content
- 60% Fewer Hallucinations
Browse by: Latest US Patents, China's latest patents, Technical Efficacy Thesaurus, Application Domain, Technology Topic, Popular Technical Reports.
© 2025 PatSnap. All rights reserved.Legal|Privacy policy|Modern Slavery Act Transparency Statement|Sitemap|About US| Contact US: help@patsnap.com