Bridge type crystal material double head grinder
A crystal material and bridge-type technology, applied in grinding machines, machine tools suitable for grinding workpiece planes, grinding/polishing equipment, etc., can solve problems such as increased processing costs, cracks in horizontal silicon core spheres, and low yields. Achieve the effect of stably grinding the ingot and improving the degree of mechanization
- Summary
- Abstract
- Description
- Claims
- Application Information
AI Technical Summary
Problems solved by technology
Method used
Image
Examples
Embodiment Construction
[0024] The present invention can be explained in more detail with reference to the following examples, but the present invention is not limited to the combination of these examples.
[0025] combined with figure 2 Or the double-head grinding machine for bridge-type crystal materials described in 3, comprising a crystal rod clamping mechanism 15; one end grinding mechanism of the crystal rod; the other end grinding mechanism of the crystal rod; the crystal rod clamping mechanism clamps the crystal rod In the middle of 18, the two grinding wheels 14 of the grinding mechanism at one end of the ingot correspond to both sides of one end of the ingot 18 respectively, and the two grinding wheels 14 are formed by the base 21 to grind the ingot 18 evenly at intervals between the two grinding wheels 14 , the rear parts of the two grinding wheels are respectively externally connected with a power mechanism or provided with a motor 24; the two grinding wheels 14 of the grinding mechanism...
PUM
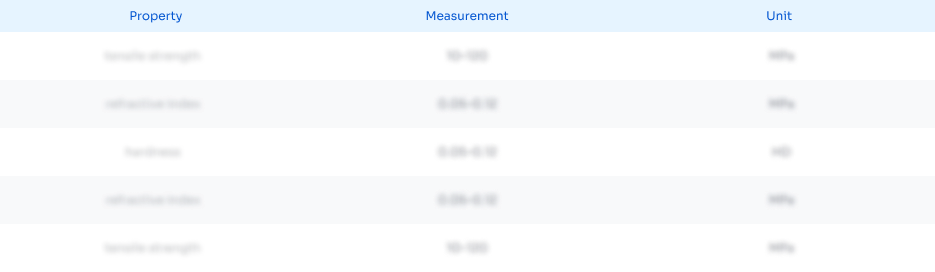
Abstract
Description
Claims
Application Information

- R&D
- Intellectual Property
- Life Sciences
- Materials
- Tech Scout
- Unparalleled Data Quality
- Higher Quality Content
- 60% Fewer Hallucinations
Browse by: Latest US Patents, China's latest patents, Technical Efficacy Thesaurus, Application Domain, Technology Topic, Popular Technical Reports.
© 2025 PatSnap. All rights reserved.Legal|Privacy policy|Modern Slavery Act Transparency Statement|Sitemap|About US| Contact US: help@patsnap.com