A treatment method for waste gas in chemical acrylamide production
A technology of acrylamide and treatment method, which is applied in the direction of chemical instruments and methods, separation methods, dispersed particle separation, etc., can solve the problems of high loss of acrylonitrile and large energy consumption, and achieve the effects of simple method, energy saving and loss reduction
- Summary
- Abstract
- Description
- Claims
- Application Information
AI Technical Summary
Problems solved by technology
Method used
Image
Examples
Embodiment Construction
[0012] Taking the exhaust gas treatment process of a chemical acrylamide plant with a daily output of 150 tons of acrylamide as an example, the present invention will be further described in detail.
[0013] refer to figure 1 . Exhaust gas adsorber No. A1, exhaust gas adsorber No. B2, exhaust gas adsorber C3, exhaust gas pre-cooler 4, primary fan 5, secondary fan 6, and recovery acrylonitrile cooler 7.
[0014] The exhaust gas precooler adopts a finned heat exchanger with a heat exchange area of 260m 2 , using cooling water at 18°C for cooling; both the primary fan and the secondary fan are centrifugal fans, with a processing capacity of 12000m 3 / h; the size of the three adsorbers of the exhaust gas adsorber is 9m in length and 2.5m in diameter, and the adsorption medium adopts sticky activated carbon fiber; the recovery acrylonitrile cooler adopts a shell-and-tube heat exchanger with a heat exchange area of 30m 2 , using cooling water at 18°C; the steam used is low-...
PUM
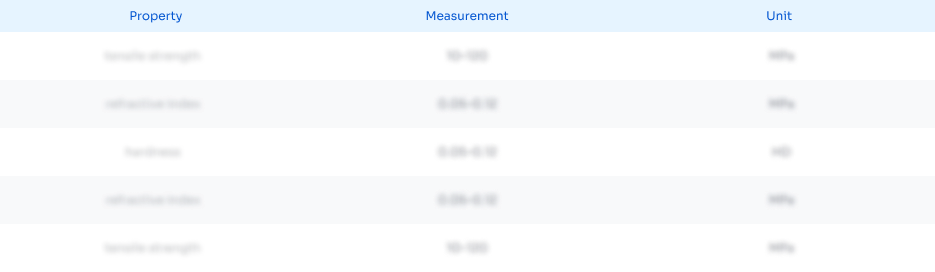
Abstract
Description
Claims
Application Information

- Generate Ideas
- Intellectual Property
- Life Sciences
- Materials
- Tech Scout
- Unparalleled Data Quality
- Higher Quality Content
- 60% Fewer Hallucinations
Browse by: Latest US Patents, China's latest patents, Technical Efficacy Thesaurus, Application Domain, Technology Topic, Popular Technical Reports.
© 2025 PatSnap. All rights reserved.Legal|Privacy policy|Modern Slavery Act Transparency Statement|Sitemap|About US| Contact US: help@patsnap.com