Preparation method of quartz crucible coating
A quartz crucible and coating technology, which is applied in the direction of coating, chemical instruments and methods, and self-melting liquid pulling method, etc., can solve the problem of single crystal edge breaking, thinning, and the service life of quartz crucible cannot meet the existing time requirements And other issues
- Summary
- Abstract
- Description
- Claims
- Application Information
AI Technical Summary
Problems solved by technology
Method used
Image
Examples
preparation example Construction
[0023] The embodiment of the invention discloses a method for preparing a barium hydroxide coating, including:
[0024] a) Prepare a barium hydroxide solution, the weight ratio of barium hydroxide to water in the barium hydroxide solution is 1: (46-52);
[0025] b) Heating the quartz crucible to above 200°C, spraying the barium hydroxide solution on the inner wall and upper mouth of the quartz crucible uniformly, and forming a barium hydroxide coating on the inner wall and upper mouth surface of the quartz crucible after spraying.
[0026] The invention adopts a spraying process to prepare barium hydroxide coating on the working surface of the quartz crucible, namely the upper mouth and the inner wall, to obtain figure 1 The quartz crucible coated with a barium hydroxide coating is shown, and the quartz crucible includes a base crucible 1 and a barium hydroxide coating 2 coated on the inner wall and upper surface of the base crucible. The formed barium hydroxide will react with carb...
Embodiment 1
[0037] 1. Use an electronic scale to weigh out 50g of deionized water and 1g of barium hydroxide, and dissolve barium hydroxide in deionized water in a nitrogen atmosphere to obtain a barium hydroxide solution;
[0038] 2. Put the 20-inch quartz crucible in an oven and heat it. After heating to 300℃, take it out and immediately spray the barium hydroxide solution configured in step 1 on the inner wall and upper mouth of the quartz crucible with a spray gun. Keep the solution on the inner wall of the crucible without The sagging phenomenon, the spraying volume of each crucible is 20.4g / 20 inch crucible, and the spraying process is completed within 2 minutes. Barium hydroxide coating is formed on the surface of the quartz crucible, the density of barium hydroxide is 0.8×10 -4 g / cm 2 .
Embodiment 2
[0040] 1. Weigh 48g deionized 1g barium hydroxide using an electronic scale, and dissolve the barium hydroxide in deionized water to obtain a barium hydroxide solution;
[0041] 2. Place the 20-inch quartz crucible in an oven and heat it to 290℃ and take it out. Immediately spray the barium hydroxide solution configured in step 1 on the inner wall and upper mouth of the quartz crucible with a spray gun. Keep the solution on the inner wall of the crucible during the spraying process. No sagging phenomenon, the spraying volume of each crucible is 19.6g / 20 inch crucible, and the spraying process is completed within 1.5min. Barium hydroxide coating is formed on the surface of the quartz crucible, and the density of barium hydroxide is 0.8×10 -4 g / cm 2 .
PUM
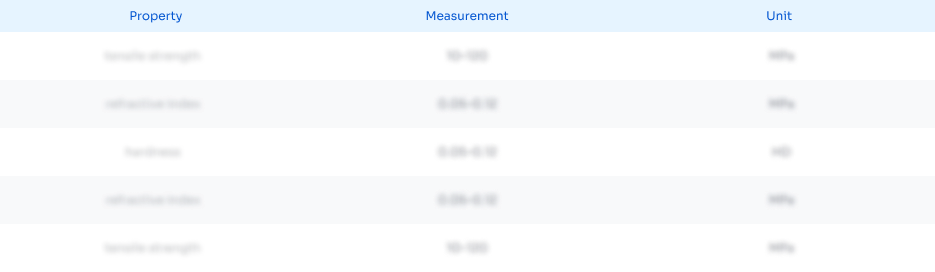
Abstract
Description
Claims
Application Information

- Generate Ideas
- Intellectual Property
- Life Sciences
- Materials
- Tech Scout
- Unparalleled Data Quality
- Higher Quality Content
- 60% Fewer Hallucinations
Browse by: Latest US Patents, China's latest patents, Technical Efficacy Thesaurus, Application Domain, Technology Topic, Popular Technical Reports.
© 2025 PatSnap. All rights reserved.Legal|Privacy policy|Modern Slavery Act Transparency Statement|Sitemap|About US| Contact US: help@patsnap.com