Process burner of water-coal slurry gasification furnace
A technology of process burners and gasifiers, which is applied in the direction of granular/powdered fuel gasification, injection devices, liquid injection devices, etc., and can solve the problems of increased investment costs and operating costs
- Summary
- Abstract
- Description
- Claims
- Application Information
AI Technical Summary
Problems solved by technology
Method used
Image
Examples
Embodiment Construction
[0015] see figure 2 , the structural form of the modified coal-water slurry gasifier process burner is also three concentric casings, that is, from the outside to the inside are the outer nozzle (outer oxygen pipe) 1, the middle nozzle (coal-water slurry pipe) 2 and the inner nozzle. The nozzle (central oxygen pipe) 3 and the outlet of the inner nozzle (central oxygen pipe) 3 are still in the form of constriction. A pre-mixing chamber 4 of coal-water slurry and central oxygen is formed, and the outlet pipeline of the coal-water slurry is also designed in a shrinking form, so that the coal-water slurry entering the pre-mixing chamber 4 has a certain speed. A cooling water coil 5 is still provided on the periphery of the outer spray head (outer oxygen pipe) 1 .
[0016] The improvement of the process burner of the existing coal-water slurry gasifier is mainly to reduce the physical wear of the inner cavity of the centering nozzle (coal-water slurry pipe) 2 during operation, an...
PUM
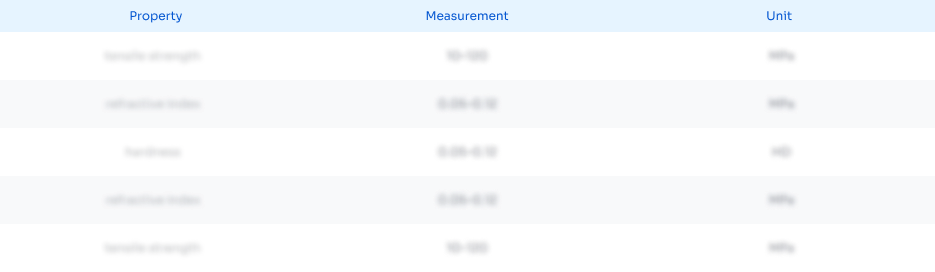
Abstract
Description
Claims
Application Information

- R&D
- Intellectual Property
- Life Sciences
- Materials
- Tech Scout
- Unparalleled Data Quality
- Higher Quality Content
- 60% Fewer Hallucinations
Browse by: Latest US Patents, China's latest patents, Technical Efficacy Thesaurus, Application Domain, Technology Topic, Popular Technical Reports.
© 2025 PatSnap. All rights reserved.Legal|Privacy policy|Modern Slavery Act Transparency Statement|Sitemap|About US| Contact US: help@patsnap.com