Cooling heat pipe heat exchanger of alumina decomposer
A technology of heat pipe heat exchanger and decomposition tank, which is applied in the field of step-by-step cooling devices, can solve problems affecting production efficiency, increasing labor time and labor intensity for scab removal, and affecting heat exchange effects, so as to improve heat exchange efficiency and work efficiency , Reduce the temperature difference between inside and outside, and enhance the service life
- Summary
- Abstract
- Description
- Claims
- Application Information
AI Technical Summary
Problems solved by technology
Method used
Image
Examples
specific Embodiment approach
[0022] figure 1 It is a structural schematic diagram of an embodiment of the present invention.
[0023] Such as figure 1 Shown: Alumina decomposition tank cooling heat pipe heat exchanger, including cooling section M and heating section L, cooling section M is fixed on a fixed bracket on the upper part of the decomposition tank (not shown in the figure), wherein cooling section M includes inner pipe 10 And the outer casing 1, the lower part of the outer casing 1 is welded with the water inlet pipe interface 2, and the top is welded with the outlet pipe interface 3, and the spiral fins 5 are welded between the outer casing 1 and the inner pipe 10 to form a spiral diversion channel 9 , so that the cooling water enters the diversion channel 9 from the water inlet pipe interface 2, spirals up, and is discharged from the water outlet pipe interface 3. The structure of the diversion channel 9 increases the stroke of the cooling water in the pipe, and plays a good heat exchange ef...
PUM
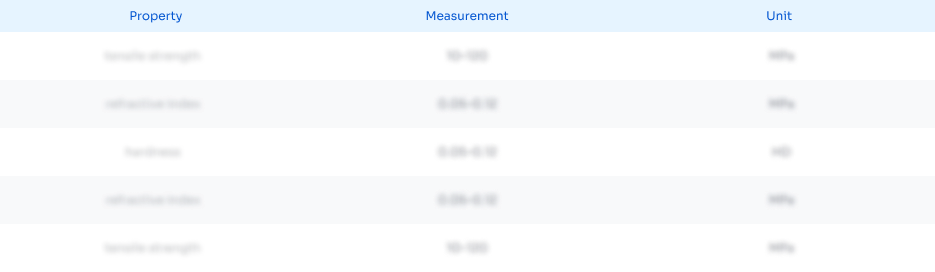
Abstract
Description
Claims
Application Information

- R&D
- Intellectual Property
- Life Sciences
- Materials
- Tech Scout
- Unparalleled Data Quality
- Higher Quality Content
- 60% Fewer Hallucinations
Browse by: Latest US Patents, China's latest patents, Technical Efficacy Thesaurus, Application Domain, Technology Topic, Popular Technical Reports.
© 2025 PatSnap. All rights reserved.Legal|Privacy policy|Modern Slavery Act Transparency Statement|Sitemap|About US| Contact US: help@patsnap.com