Compression spring processing process
A processing technology, a technology for compressing springs, applied in the direction of wire processing, wire manufacturing springs, manufacturing tools, etc., can solve problems such as large pitch, unguaranteed spring load, and impact on spring production progress.
- Summary
- Abstract
- Description
- Claims
- Application Information
AI Technical Summary
Problems solved by technology
Method used
Examples
Embodiment Construction
[0010] A compression spring processing technology is characterized in that the process steps are as follows:
[0011] 1) Rolling: Coil the cored spring on the lathe, and ensure the technical parameters of the outer diameter, pitch, length, working ring, supporting ring and total number of turns of the supporting ring;
[0012] 2) Broken circle: use broken thread scissors to break the working circle and the total circle according to the process requirements;
[0013] 3) Diameter reduction: install the spring on Figure 1 On the special tool shown, the support ring is fixed on the big end of the mandrel, and the working ring of the spring is wound on the small diameter at the same time, so as to reduce the outer diameter of the working ring of the spring;
[0014] 4) Quenching: heat in a salt bath furnace at 850±10°C, keep it warm for 7-8 minutes, and then cool in oil at 20-100°C;
[0015] 5) Primary tempering: heating in the furnace at 430-520°C and holding for 60 minutes;
...
PUM
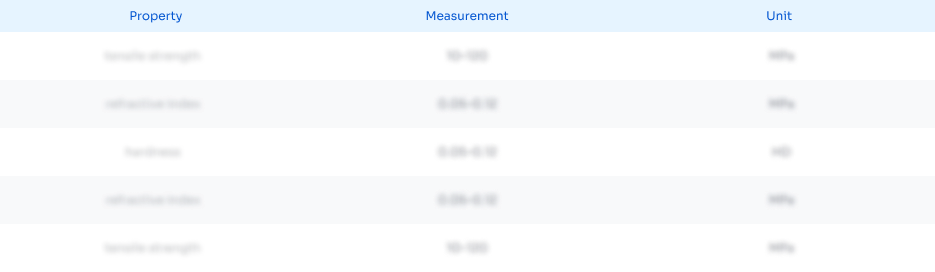
Abstract
Description
Claims
Application Information

- R&D
- Intellectual Property
- Life Sciences
- Materials
- Tech Scout
- Unparalleled Data Quality
- Higher Quality Content
- 60% Fewer Hallucinations
Browse by: Latest US Patents, China's latest patents, Technical Efficacy Thesaurus, Application Domain, Technology Topic, Popular Technical Reports.
© 2025 PatSnap. All rights reserved.Legal|Privacy policy|Modern Slavery Act Transparency Statement|Sitemap|About US| Contact US: help@patsnap.com