Wet strength waste paper processing method
A processing method and technology for waste paper, applied in the field of papermaking, can solve the problems of poor product absorption and air permeability, color change by chemical method, long processing time, etc., and achieve the effect of shortening processing time, stable percussion degree, and shortening processing time.
- Summary
- Abstract
- Description
- Claims
- Application Information
AI Technical Summary
Problems solved by technology
Method used
Image
Examples
Embodiment
[0022] As shown in the process flow chart: steam condensed water is used as the heat source, a heat exchanger is added to keep the water temperature at 65°C, and the processing time of the pulping process is shortened to 30 minutes. The specific process steps are as follows:
[0023] 1. Pulping: Mix the waste paper with white water heated at 66°C, and perform hydropulping at a concentration of 4.3% for 40 minutes, and then store it in the pulp tank for future use;
[0024] 2. Refining: Lift the raw materials in the storage tank to the refiner for refining. The processing time is controlled at 45 minutes according to the wet strength of waste paper, and the degree of knocking is 33 O SR, wet weight 5g;
[0025] 3. Blending pulp: the blending ratio is 18%.
PUM
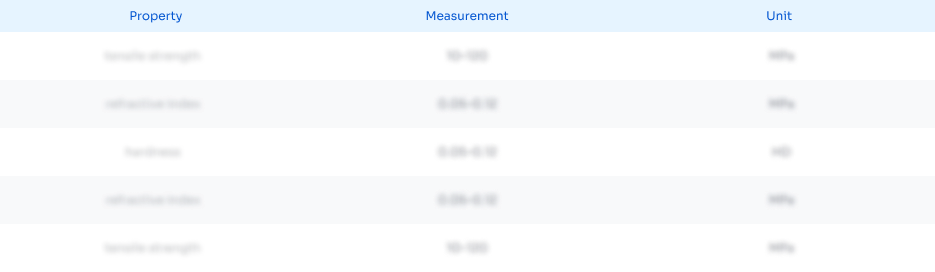
Abstract
Description
Claims
Application Information

- R&D
- Intellectual Property
- Life Sciences
- Materials
- Tech Scout
- Unparalleled Data Quality
- Higher Quality Content
- 60% Fewer Hallucinations
Browse by: Latest US Patents, China's latest patents, Technical Efficacy Thesaurus, Application Domain, Technology Topic, Popular Technical Reports.
© 2025 PatSnap. All rights reserved.Legal|Privacy policy|Modern Slavery Act Transparency Statement|Sitemap|About US| Contact US: help@patsnap.com