Fine forging forming method of spiral bevel gears
A manufacturing method and gear precision technology, applied in the direction of manufacturing tools, forging/pressing/hammering machinery, wheels, etc., can solve the problems of short mold life, arc tooth damage, arc tooth profile damage, etc., to prolong the service life, Effect of reducing radial flow and improving life
- Summary
- Abstract
- Description
- Claims
- Application Information
AI Technical Summary
Problems solved by technology
Method used
Image
Examples
Embodiment Construction
[0030] The precision forging and forming manufacturing method of spiral bevel gear of the present invention is characterized in that comprising the following steps:
[0031] (1) Prepare raw materials according to the process design requirements, grind the surface of the raw materials, inspect the cracks, and then saw them into material sections, and remove the material sections that do not meet the requirements; the grinding surface, flaw detection inspection, etc., all adopt the existing technology, here no further description;
[0032] (2) Heat the material section to 1150-1180°C, specifically, it can be heated in an intermediate frequency induction furnace;
[0033] (3) Pier the material section on the press, punch holes, and then expand the ring through the ring rolling machine to obtain a ring-shaped blank;
[0034] (4) Set the ring-shaped blank on a multi-station hot die forging press, and pre-forge it in the pre-forging die to obtain a pre-forging blank with a pr...
PUM
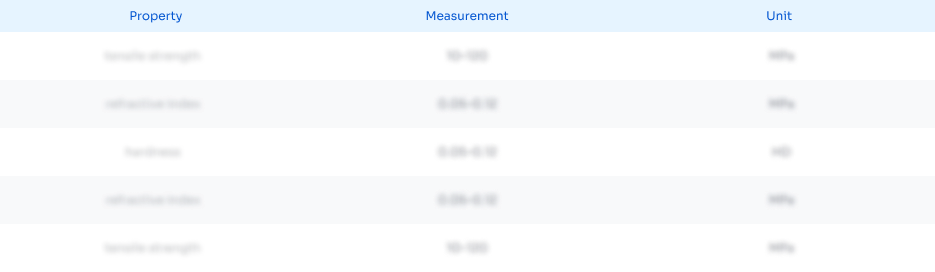
Abstract
Description
Claims
Application Information

- R&D Engineer
- R&D Manager
- IP Professional
- Industry Leading Data Capabilities
- Powerful AI technology
- Patent DNA Extraction
Browse by: Latest US Patents, China's latest patents, Technical Efficacy Thesaurus, Application Domain, Technology Topic, Popular Technical Reports.
© 2024 PatSnap. All rights reserved.Legal|Privacy policy|Modern Slavery Act Transparency Statement|Sitemap|About US| Contact US: help@patsnap.com