Laser interference lithographic system
A laser interference lithography and photolithography technology, applied in the field of micro-nano structure manufacturing, can solve the problems of small adjustment range of interference beam angle, limited interference pattern diversity, complex optical path system, etc., to reduce optical path loss, meet the diversity, The effect of increasing the adjustment range
- Summary
- Abstract
- Description
- Claims
- Application Information
AI Technical Summary
Problems solved by technology
Method used
Image
Examples
Embodiment 1
[0039] see image 3 , is a structural diagram of a laser interference lithography system disclosed in Embodiment 1 of the present invention. like figure 1 As shown, the system includes: four mirror groups. The first mirror group comprises: beam splitter 1011, the first total reflection mirror 1012 and the second total reflection mirror 1013; the second mirror group comprises: beam splitter 1021, the first total reflection mirror 1022 and the second total reflection mirror 1023; the third The mirror group includes: a beam splitter 1031 , a first total reflection mirror 1032 and a second total reflection mirror 1033 ; the fourth mirror group includes: a beam splitter 1041 , a first total reflection mirror 1042 and a second total reflection mirror 1043 .
[0040] The beam splitters of each mirror group are located on the main optical axis of the incident light. The first lens group to the fourth lens group are sequentially arranged on the main optical axis in order of distance...
Embodiment 2
[0057] see Figure 4 , is a structural diagram of the laser interference lithography system disclosed in Embodiment 2 of the present invention. like Figure 4 As shown, the system includes: a first type-one mirror group composed of a beam splitter 2011, a total reflection mirror 2012 and a total reflection mirror 2013; a second type-one mirror group composed of a beam splitter 2021, a total reflection mirror 2022 and a total reflection mirror 2023 The third one-type mirror group that beam splitter 2031, total reflection mirror 2032 and total reflection mirror 2033 constitute; the second type mirror group that total reflection mirror 2041,2042,2043 forms.
[0058] Wherein, the beam splitter 2011 of the first type I mirror group, the beam splitter 2021 of the second type I mirror group, the beam splitter 2031 of the third type I mirror group and the total reflection mirror 2041 of the second type mirror group are all positioned at the center of the incident light on the princi...
PUM
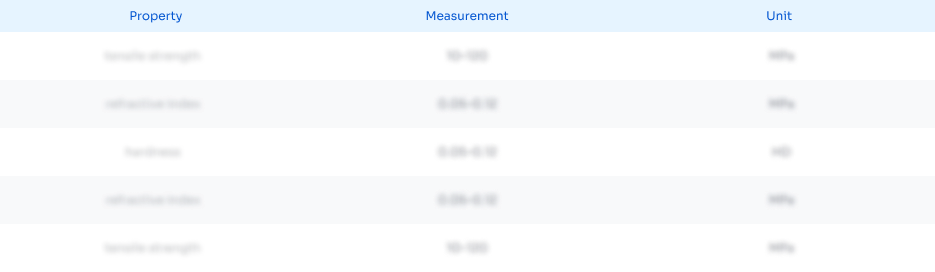
Abstract
Description
Claims
Application Information

- R&D
- Intellectual Property
- Life Sciences
- Materials
- Tech Scout
- Unparalleled Data Quality
- Higher Quality Content
- 60% Fewer Hallucinations
Browse by: Latest US Patents, China's latest patents, Technical Efficacy Thesaurus, Application Domain, Technology Topic, Popular Technical Reports.
© 2025 PatSnap. All rights reserved.Legal|Privacy policy|Modern Slavery Act Transparency Statement|Sitemap|About US| Contact US: help@patsnap.com