Method for setting width of ferrite stainless steel slab during continuous casting production
A setting method, ferrite technology, applied in the field of metallurgy, can solve problems such as unstable slab width
- Summary
- Abstract
- Description
- Claims
- Application Information
AI Technical Summary
Problems solved by technology
Method used
Image
Examples
Embodiment 1
[0053] In this embodiment, ferritic stainless steel SUS410S is selected, and the target width of the slab is W Cold is 1265mm, then to obtain a ferritic stainless steel slab that meets the requirements, proceed through the following steps:
[0054] (1) Calculate the shrinkage rate in the width direction of the ferritic stainless steel SUS410S slab from the temperature at the outlet of the continuous casting machine crystallizer to the temperature when it is cooled to room temperature
[0055] W T = W Mold ∫ T cold T M - ex α ( T ) dT - - - ( 1 . ...
PUM
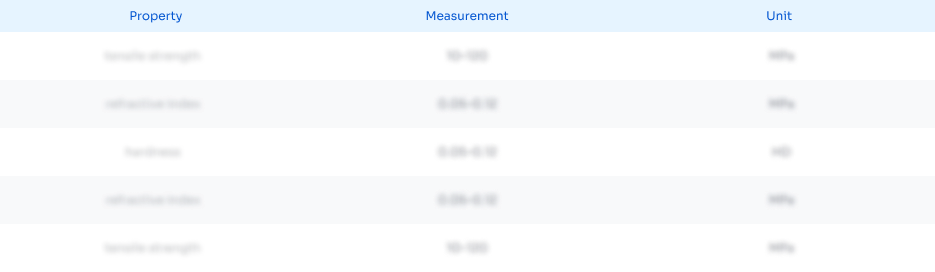
Abstract
Description
Claims
Application Information

- Generate Ideas
- Intellectual Property
- Life Sciences
- Materials
- Tech Scout
- Unparalleled Data Quality
- Higher Quality Content
- 60% Fewer Hallucinations
Browse by: Latest US Patents, China's latest patents, Technical Efficacy Thesaurus, Application Domain, Technology Topic, Popular Technical Reports.
© 2025 PatSnap. All rights reserved.Legal|Privacy policy|Modern Slavery Act Transparency Statement|Sitemap|About US| Contact US: help@patsnap.com