Novel separation process of multi-metal lean hematite
A polymetallic and hematite technology, applied in flotation, solid separation, wet separation, etc., can solve the problem of unsatisfactory separation index, achieve effective separation and improve the quality of concentrate
- Summary
- Abstract
- Description
- Claims
- Application Information
AI Technical Summary
Problems solved by technology
Method used
Image
Examples
Embodiment Construction
[0023] The specific implementation of the present invention will be described in detail below in conjunction with the examples.
[0024] Such as figure 1 Shown, the sorting new technology of polymetallic poor hematite of the present invention is characterized in that comprising the following steps:
[0025] 1) After the polymetallic symbiotic lean hematite ore passes through the closed-circuit grinding formed by the primary ball mill 1 and the primary classification 2, the overflow of the primary classification 2 is fed into the secondary classification 3,
[0026] 2) The grit of the secondary classification 3 is fed into the secondary ball mill 4, and the ore row of the secondary ball mill 4 is returned to the secondary classification 3 for classification.
[0027] 3) The overflow of secondary classification 3 is fed into a section of weak magnetic separation 5,
[0028] 4) One stage of weak magnetic separation 5 selects some magnetic iron minerals, and the tailings selecte...
PUM
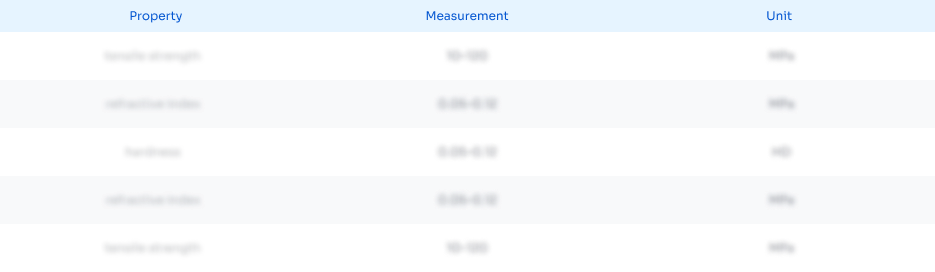
Abstract
Description
Claims
Application Information

- R&D Engineer
- R&D Manager
- IP Professional
- Industry Leading Data Capabilities
- Powerful AI technology
- Patent DNA Extraction
Browse by: Latest US Patents, China's latest patents, Technical Efficacy Thesaurus, Application Domain, Technology Topic, Popular Technical Reports.
© 2024 PatSnap. All rights reserved.Legal|Privacy policy|Modern Slavery Act Transparency Statement|Sitemap|About US| Contact US: help@patsnap.com