Combined ore-dressing method for recovering superfine cassiterite from oxidized tin tailings
A beneficiation method and oxidation-type technology, applied in chemical instruments and methods, wet separation, solid separation, etc., can solve the problems of complex components, large mud content, low grade, etc., and achieve simple process, high recovery rate, and total low cost effect
- Summary
- Abstract
- Description
- Claims
- Application Information
AI Technical Summary
Problems solved by technology
Method used
Examples
Embodiment example 1
[0023] The content of -0.037mm particle size accounted for 100% (of which -5 micron particle size accounted for 28.7%), the tin grade was 0.156%, the Fe grade was 10.8%, the CaO content was 16.6%, the MgO content was 11.3%, and the SiO content was 11.3%. 2 Tailings with a content of 15.6%.
[0024] A. Add 500g of polyacrylamide per ton of the above-mentioned tin-containing tailings and mix to obtain the slurry material;
[0025] B. The ore slurry material of step A was stirred for 5 minutes, to form condensed tin mineral;
[0026] C. The condensed tin minerals in step B are subjected to gravity separation and enrichment to obtain tin middlings and tailings.
[0027] The obtained middling tin grade and recovery rate were 2.68% and 63.60%, respectively. After adding the agent, the recovery rate of tin can be increased by 15-20 percentage points.
Embodiment example 2
[0029] The content of -0.037mm particle size accounted for 100% (of which -5 micron particle size accounted for 23.7%), the grade of tin was 0.165%, the grade of Fe was 9.7%, the content of CaO was 14.5%, the content of MgO was 8.6%, and the content of SiO 2 Tin tailings with a content of 18.7%.
[0030] A. Add 850g of oleic acid and sodium chloride per ton of the above-mentioned tin-containing tailings for mixing to obtain a slurry material;
[0031] B. The ore slurry material of step A was stirred for 4 minutes to form condensed tin minerals;
[0032] C. The condensed tin minerals in step B are subjected to gravity separation and enrichment to obtain tin middlings and tailings.
[0033] The obtained middling tin grade and recovery rate were 2.98% and 62.55%, respectively. After adding the agent, the recovery rate of tin is increased by 16.2-19.5 percentage points.
Embodiment example 3
[0035] The content of -0.037mm particle size accounted for 100% (of which -5 micron particle size accounted for 16.8%), the grade of tin was 0.253%, the grade of Fe was 11.4%, the content of CaO was 13.1%, the content of MgO was 9.4%, and the content of SiO 2 Tailings with a content of 19.2%.
[0036] A. Add 1500g of polynuclear polysilicic acid, sodium sulfide, sodium hydroxide and sodium silicate to the above-mentioned tin-containing tailings per ton and mix to obtain the pulp material;
[0037] B. The ore slurry material of step A was stirred for 3 minutes, to form condensed tin mineral;
[0038] C. The condensed tin minerals in step B are subjected to gravity separation and enrichment to obtain tin middlings and tailings.
[0039] The obtained middling tin grade and recovery rate were 3.36% and 60.28%, respectively. After adding the agent, the recovery rate of tin is increased by 15.3-19.8 percentage points.
PUM
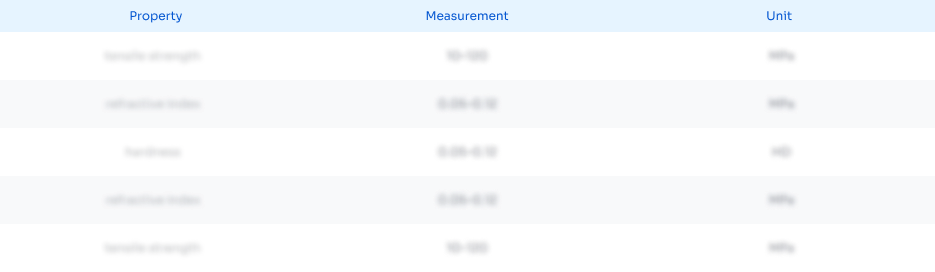
Abstract
Description
Claims
Application Information

- Generate Ideas
- Intellectual Property
- Life Sciences
- Materials
- Tech Scout
- Unparalleled Data Quality
- Higher Quality Content
- 60% Fewer Hallucinations
Browse by: Latest US Patents, China's latest patents, Technical Efficacy Thesaurus, Application Domain, Technology Topic, Popular Technical Reports.
© 2025 PatSnap. All rights reserved.Legal|Privacy policy|Modern Slavery Act Transparency Statement|Sitemap|About US| Contact US: help@patsnap.com