Method for producing paper pulp by oxidatively bursting wall of straw
A technology of straw and oxygen explosion, applied to the separation of raw materials, etc., can solve the problems of large water consumption, expansion of production scale, difficult sewage treatment, etc., and achieve the effect of reduced stacking volume, low production cost, and thorough decomposition
- Summary
- Abstract
- Description
- Claims
- Application Information
AI Technical Summary
Problems solved by technology
Method used
Image
Examples
Embodiment 1
[0020] The method for making paper pulp by oxygen blasting wall straw of the present invention comprises the following steps:
[0021] A, prepare the stalk of raw material biomass, and crush it to below 50mm;
[0022] B. Add 5kg or 8kg or 10kg or 15kg or 18kg or 23kg or 26kg or 29kg or 32kg or 38kg or 40kg or 45kg or 48kg or 53kg or 56kg or 59kg or 62kg or 65kg to the crushed straw according to the weight of 200kg of straw Or 68kg or 73kg or 76kg or 79kg or 80kg parts by weight of liquid ammonia, 1kg or 2kg or 5kg or 8kg or 10kg or 15kg or 18kg or 20kg parts by weight of urea, 1kg or 2kg or 4kg or 7kg or 10kg or 14kg or 17kg or 20kg of 35% concentration of hydrogen peroxide and 5kg or 7kg or 9kg or 13kg or 16kg or 23kg or 27kg or 29kg or 33kg or 38kg or 40kg or 45kg or 48kg or 53kg or 56kg or 59kg or 62kg or 65kg or 68kg or 73kg or 76kg or 79kg or 80kg of water by weight, add liquid ammonia, urea, 35% concentration of hydrogen peroxide and water, and then stir the material fo...
Embodiment 2
[0033] The method for making paper pulp by oxygen blasting wall straw of the present invention comprises the following steps:
[0034] A. Prepare the stalk of raw material biomass and crush it to 1-50mm;
[0035] B, the stalk after pulverizing is according to the stalk of 200kg weight part, correspondingly adds the liquefied ammonia of 10kg weight part, the urea of 10kg weight part, the hydrogen peroxide of 35% concentration of 10kg weight part, the sodium hydroxide of 10kg weight part, 10kg weight part Potassium hydroxide, the calcium hydroxide of 10kg parts by weight and the water of 50kg parts by weight, then the material is stirred for 3 minutes, allowing the material to be subjected to oxidation-soaking treatment;
[0036] C. The material after oxidation-soaking treatment is transported to the oxygen explosion tank through the feed port of the oxygen explosion tank for compaction and filling. After filling, the feed port of the oxygen explosion tank is closed, and then ...
Embodiment 3
[0042] The method for making paper pulp by oxygen blasting wall straw of the present invention comprises the following steps:
[0043] A. Prepare the stalk of raw material biomass and crush it to 1-50mm;
[0044] B, the stalk after pulverizing is according to the stalk of 200kg weight part, correspondingly adds the liquefied ammonia of 5kg weight part, the urea of 15kg weight part, the hydrogen peroxide of 35% concentration of 12kg weight part, the sodium hydroxide of 5kg weight part, 5kg weight part Potassium hydroxide, the calcium hydroxide of 5kg parts by weight and the water of 60kg parts by weight, then the material is stirred for 2 minutes, allowing the material to be subjected to oxidation-soaking treatment;
[0045] C. The material after oxidation-soaking treatment is transported to the oxygen explosion tank through the feed port of the oxygen explosion tank for compaction and filling. After filling, the feed port of the oxygen explosion tank is closed, and then satu...
PUM
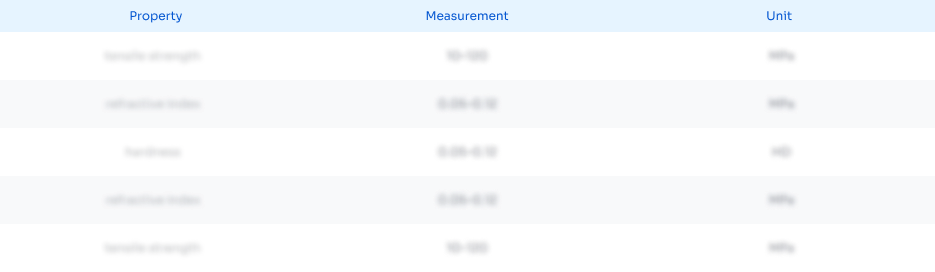
Abstract
Description
Claims
Application Information

- Generate Ideas
- Intellectual Property
- Life Sciences
- Materials
- Tech Scout
- Unparalleled Data Quality
- Higher Quality Content
- 60% Fewer Hallucinations
Browse by: Latest US Patents, China's latest patents, Technical Efficacy Thesaurus, Application Domain, Technology Topic, Popular Technical Reports.
© 2025 PatSnap. All rights reserved.Legal|Privacy policy|Modern Slavery Act Transparency Statement|Sitemap|About US| Contact US: help@patsnap.com