Preparation method of allyl polyether
An allyl polyether and allyl technology, which is applied in the field of preparation of allyl polyether, can solve the problems of large amount of catalyst, wide molecular weight distribution, and large loss of double bonds, etc., and achieve narrow molecular weight distribution, double bond Effect of high key value and low quality score
- Summary
- Abstract
- Description
- Claims
- Application Information
AI Technical Summary
Problems solved by technology
Method used
Image
Examples
Embodiment 1
[0026] Add 116g of allyl alcohol (purity 99.5%, distilled before use) and 0.864g of catalyst A (the catalyst mass fraction based on the final product is 30×10) into a 3L autoclave -6 ), the temperature is increased to 90±1℃, and 180g of propylene oxide is continuously added slowly to induce the reaction; when the pressure in the kettle has dropped significantly and the catalyst has been activated, continue to add 304g of propylene oxide and maintain the pressure less than 0.15MPa during the feeding process At this time, the design molecular weight of allyl polyether in the reactor is 300; take out 550g allyl-propylene oxide oligomer, and continuously add 25.13g allyl alcohol / 1.32g polymerization stabilizer H / 2324.87 to the remaining 50g g Propylene oxide mixture, maintain the pressure below 0.15MPa during the feeding process, and stop feeding when the added reaction material reaches the designed amount. When the pressure in the kettle does not change significantly, the reaction ...
Embodiment 2
[0028] Catalyst B replaces catalyst A, and the rest is the same as in Example 1.
Embodiment 3
[0030] Catalyst C replaces Catalyst A, and the rest is the same as in Example 1.
PUM
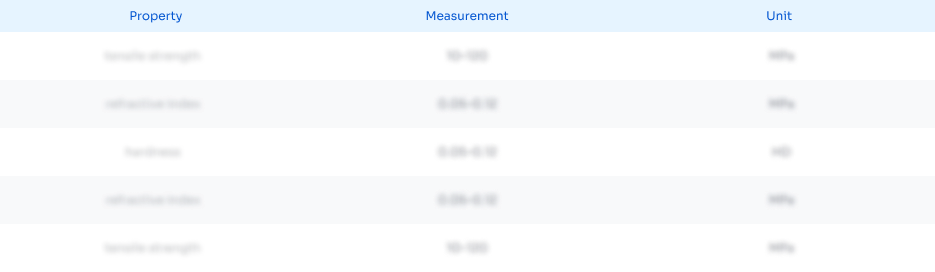
Abstract
Description
Claims
Application Information

- R&D
- Intellectual Property
- Life Sciences
- Materials
- Tech Scout
- Unparalleled Data Quality
- Higher Quality Content
- 60% Fewer Hallucinations
Browse by: Latest US Patents, China's latest patents, Technical Efficacy Thesaurus, Application Domain, Technology Topic, Popular Technical Reports.
© 2025 PatSnap. All rights reserved.Legal|Privacy policy|Modern Slavery Act Transparency Statement|Sitemap|About US| Contact US: help@patsnap.com