Method for reinforcing fast-growing floor board
A technology for enhancing processing and floor materials, applied in wood processing, wood processing details, wood processing equipment, etc., can solve the problems of not being able to increase the density of wood, and not be able to effectively curb the rebound of the board, and achieve the effect of low density and high elasticity
- Summary
- Abstract
- Description
- Claims
- Application Information
AI Technical Summary
Problems solved by technology
Method used
Examples
Embodiment 1
[0026] Example 1: only densification
[0027] Fast-growing poplar (Poplus deltoides) is used as the substrate, with a format of 600mm×150mm and a thickness of 12mm. Use a hot press to carry out compaction at a temperature of 100°C, a pressure of 1 MPa, and spray 1 g of water on the surface of the board for 5 minutes (press immediately after spraying water, the purpose is to generate water vapor on the surface of the board, plasticize the wood, and facilitate compaction and setting. The rebound is better than not spraying water), the degree of compression is 13.5% after compaction, and 55% in the middle of the thickness direction is not compressed. The surface hardness of the board after compaction reaches 15.84Mpa (the surface hardness is 11.5Mpa when untreated). The plate is aged for 30 days under the conditions of 20° C. and 65% humidity, and the thickness rebound rate of the plate is lower than 4%.
Embodiment 2
[0028] Example 2: carbonization after densification
[0029] Fast-growing poplar is used as the base material, with a format of 600mm×150mm and a thickness of 12mm. After compaction at 100°C, 1MPa and 1g of water spray for 5min (densification conditions and compression degree are the same as in Example 1), immediately carbonize at 240°C and 1.0MPa for 60s. The surface color of the carbonized board becomes darker, and the surface hardness of the board reaches 19.4Mpa, which is 68.7% higher than that of untreated fast-growing poplar. After aging for 30 days at 20°C and 65% humidity, the rebound rate of the plate thickness is close to 0.
Embodiment 3
[0030] Example 3: Comprehensive treatment of "densification + carbonization + nitriding"
[0031] Fast-growing poplar is used as the base material, with a format of 600mm×150mm and a thickness of 12mm. Use a hot press to densify at 100°C, 1MPa, and spray 1g of water for 5 minutes and then carry out carbonization treatment at 240°C (the conditions of densification and carbonization and the degree of compression are the same as in Example 2), and then perform plasma nitriding treatment (using radio frequency plasma Body processor, plasma atmosphere is nitrogen, vacuum degree: 50Pa; power: 300W; time: 7min). After treatment, the board hardness reaches 21MPa, which is 82.6%, 32.6% and 8.2% higher than that of untreated fast-growing poplar wood, dense wood (Example 1) and dense carbonized wood (Example 2). After aging for 30 days at 20°C and 65% humidity, the thickness rebound rate of the board is close to 0.
PUM
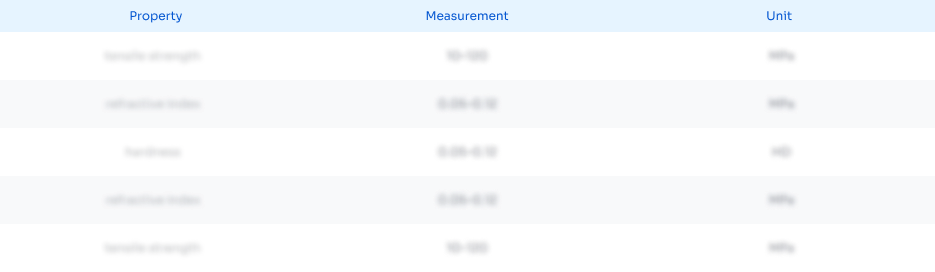
Abstract
Description
Claims
Application Information

- Generate Ideas
- Intellectual Property
- Life Sciences
- Materials
- Tech Scout
- Unparalleled Data Quality
- Higher Quality Content
- 60% Fewer Hallucinations
Browse by: Latest US Patents, China's latest patents, Technical Efficacy Thesaurus, Application Domain, Technology Topic, Popular Technical Reports.
© 2025 PatSnap. All rights reserved.Legal|Privacy policy|Modern Slavery Act Transparency Statement|Sitemap|About US| Contact US: help@patsnap.com