Step recycling method and device of boiler flue gas waste heat
A cascade recovery and boiler flue gas technology, which is applied in steam engine installations, climate sustainability, sustainable manufacturing/processing, etc., can solve problems such as forced shutdown, aggravated pipeline heating surface wear, and increased flue resistance, achieving safety High performance and reduced risk of tube clogging due to dust accumulation
- Summary
- Abstract
- Description
- Claims
- Application Information
AI Technical Summary
Problems solved by technology
Method used
Image
Examples
specific Embodiment 1
[0055] like Figure 7 As shown, the flue gas waste heat recovery device is divided into two stages and arranged in the boiler tail flue and desulfurization flue. The first-stage heat exchanger 31 is arranged between the desulfurization system booster fan 60 and the absorption tower 70, and the second-stage heat exchanger 32 is arranged between the outlet of the air preheater 20 and the inlet of the dust collector 40 in the tail flue of the boiler .
[0056] In the desulfurization area, there is also a bypass flue gas channel connected from the outlet of the induced draft fan 50 to the chimney 80, a desulfurization bypass baffle 84 is provided in the bypass flue gas channel, and an inlet baffle 82 is provided at the inlet of the booster fan 60 , the outlet of the absorption tower 70 is provided with an outlet baffle 86; when the first-stage heat exchanger 31 or other components in the desulfurization area fail, the desulfurization bypass baffle 84 is opened, the inlet baffle 8...
specific Embodiment 2
[0064] like Figure 8 As shown, with the continuous improvement of the country's requirements for environmental protection facilities, it has become a major trend in the future that the desulfurization system of the thermal power unit is not equipped with a bypass. The idea of the present invention is also applicable to units that are not equipped with a desulfurization bypass.
[0065] The flue gas waste heat recovery device is also divided into two stages and arranged in the flue and the desulfurization flue at the tail of the boiler 10 . The first-stage heat exchanger 31 is arranged between the desulfurization system booster fan and the absorption tower, and the second-stage heat exchanger 32 is arranged between the outlet of the air preheater and the inlet of the dust collector in the tail flue of the boiler.
[0066] The flow of the flue gas side of the flue gas waste heat recovery device is as follows: the flue gas discharged from the boiler 10 passes through the air p...
specific Embodiment 3
[0068] like Figure 9 As shown, the flue gas waste heat recovery device is divided into three stages and arranged in the boiler tail flue and desulfurization flue. The first-stage heat exchanger 31 is arranged between the desulfurization system booster fan 60 and the absorption tower 70, and the second-stage heat exchanger 32 is arranged between the outlet of the air preheater 20 and the inlet of the dust collector 40 in the tail flue of the boiler , an intermediate stage heat exchanger 33 is added, arranged in the flue between the outlet of the induced draft fan 50 and the inlet of the booster fan 60 .
[0069] The flow of the flue gas side in the flue gas waste heat recovery device is as follows: the flue gas discharged from the boiler 10 passes through the air preheater 20, enters the second-stage heat exchanger 32 to release part of the heat, and then passes through the dust collector 40 and the induced draft fan 50 to perform work , the temperature of the flue gas is inc...
PUM
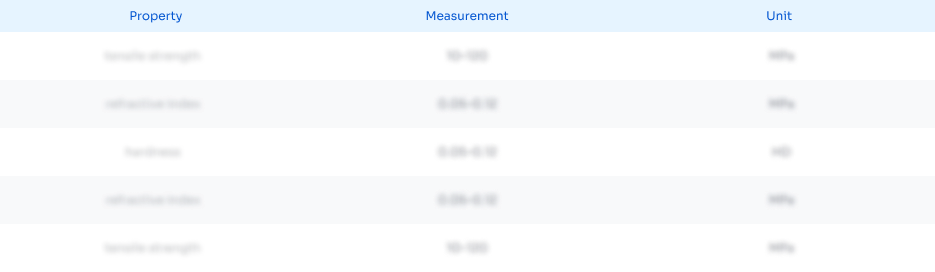
Abstract
Description
Claims
Application Information

- R&D
- Intellectual Property
- Life Sciences
- Materials
- Tech Scout
- Unparalleled Data Quality
- Higher Quality Content
- 60% Fewer Hallucinations
Browse by: Latest US Patents, China's latest patents, Technical Efficacy Thesaurus, Application Domain, Technology Topic, Popular Technical Reports.
© 2025 PatSnap. All rights reserved.Legal|Privacy policy|Modern Slavery Act Transparency Statement|Sitemap|About US| Contact US: help@patsnap.com