Polyurethane resin for high-density shoe leather and preparation method thereof
A high-density, wet-process polyurethane technology, used in textiles and papermaking, etc., can solve the problems of slow solidification speed of coating slurry, low solid content of impregnating material, and difference in solidification speed, etc. Penetration, the effect of reducing the difference in penetration speed
- Summary
- Abstract
- Description
- Claims
- Application Information
AI Technical Summary
Problems solved by technology
Method used
Examples
Embodiment 1
[0024] Raw material name Weight (kg)
[0025] Polytetrahydrofuran oxide ethylene copolymer glycol (number average molecular weight 2000) 920
[0026] Polyoxypropylene diol (number average molecular weight 3000) 1380
[0027] MDI (diphenylmethane-4,4`-diisocyanate) 953.63
[0028] EG (ethylene glycol) 179.46
[0029] Antioxidant TPP 5.1
[0030] Catalyst (bismuth carboxylate) 0.051
[0031] DMF (N, N-dimethylformamide) 6664.25
Embodiment 2
[0033] Raw material name Weight (kg)
[0034] Polytetrahydrofuran oxide ethylene copolymer glycol (number average molecular weight 1000) 1125
[0035] Polyoxypropylene diol (number average molecular weight 2000) 1125
[0036] MDI (diphenylmethane-4,4`-diisocyanate) 989.68
[0037] BG (1,4 butanediol) 204.4
[0038] Antioxidant TPP 5.1
[0039] Catalyst (bismuth carboxylate) 0.051
[0040] DMF (N, N-dimethylformamide) 6685.59
Embodiment 3
[0042] Raw material name Weight (kg)
[0043] Polytetrahydrofuran oxide ethylene copolymer glycol (number average molecular weight 2000) 920
[0044] Polyoxypropylene diol (number average molecular weight 3000) 1380
[0045] MDI (phenylmethane-4,4`-diisocyanate) 1006.35
[0046] EG (ethylene glycol) 144.4
[0047] 1,6-HG (1,6-hexanediol) 208.26
[0048] Antioxidant TPP 5.2
[0049] Catalyst (bismuth carboxylate) 0.052
[0050] DMF (N, N-dimethylformamide) 6876.35
PUM
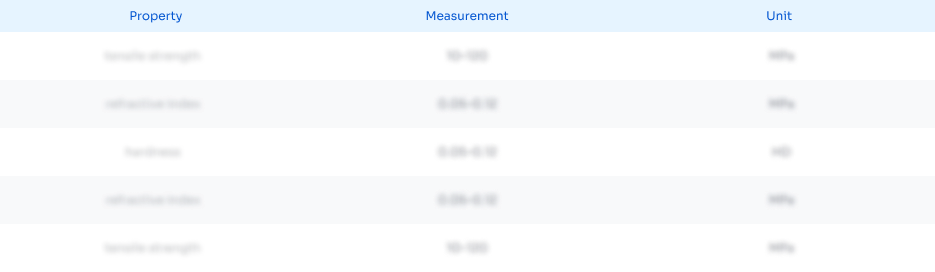
Abstract
Description
Claims
Application Information

- R&D
- Intellectual Property
- Life Sciences
- Materials
- Tech Scout
- Unparalleled Data Quality
- Higher Quality Content
- 60% Fewer Hallucinations
Browse by: Latest US Patents, China's latest patents, Technical Efficacy Thesaurus, Application Domain, Technology Topic, Popular Technical Reports.
© 2025 PatSnap. All rights reserved.Legal|Privacy policy|Modern Slavery Act Transparency Statement|Sitemap|About US| Contact US: help@patsnap.com