Forming die and forming method for nano-diaphragm special for filter press
A diaphragm and forming mold technology, which is applied in the field of filter press diaphragm forming mold manufacturing, can solve the problems that the nano-diaphragm filter cannot be formed, achieve good anti-fouling properties, eliminate static electricity, and not easy to absorb.
- Summary
- Abstract
- Description
- Claims
- Application Information
AI Technical Summary
Problems solved by technology
Method used
Image
Examples
Embodiment 1
[0011] Embodiment 1: with reference to attached Figure 1-3 . A special nano-diaphragm forming mold for filter presses, which includes an upper mold 3 and a lower mold 1. There are multiple heating channels around the lower mold 1 and heating elements 4 are built in the heating channels. The molding surface of the upper mold 3 is A plurality of nozzles 7 are provided and the nozzles 7 communicate with the nano pressurizer 6 through the fluid channel 5 in the upper mold 3 body. The manufacture of the upper mold 3 and the lower mold 1 is a prior art, and will not be described here. Nano pressurization (jet) device 6 is prior art, does not describe at this.
[0012] The heating element 4 is an electric heating tube or an electric heating wire, and the installation of the electric heating tube or the electric heating wire and the heating channel in the lower mold 1 and the design of the electric heating tube or the electric heating wire terminal connected to the power control end...
Embodiment 2
[0015] Embodiment 2: On the basis of embodiment 1, the molding method of the special nano-diaphragm sheet molding mold for filter press, first the diaphragm light sheet after molding is placed in the lower film after heating, when the diaphragm light sheet positioned in the lower mold cavity When the sheet has just passed the critical point of melting, start the nano pressurizer 6, and the multiple nozzles 7 on the forming die surface of the upper mold 3 above the lower mold spray the nanomaterials onto the surface of the diaphragm light sheet, and then pressurize and close The upper mold forces the nano-layer sprayed on the diaphragm to blend into the surface of the diaphragm, and the nano-diaphragm is obtained after cooling. The pressure ejected from the nozzle 7 is greater than or equal to the pressure exerted by the upper die on the diaphragm. The nano material is nano ceramic powder, nano metal material. The nanolayer is larger than 0.1 microns.
PUM
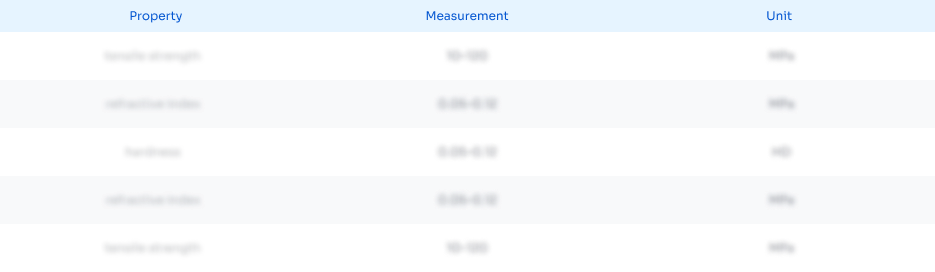
Abstract
Description
Claims
Application Information

- R&D
- Intellectual Property
- Life Sciences
- Materials
- Tech Scout
- Unparalleled Data Quality
- Higher Quality Content
- 60% Fewer Hallucinations
Browse by: Latest US Patents, China's latest patents, Technical Efficacy Thesaurus, Application Domain, Technology Topic, Popular Technical Reports.
© 2025 PatSnap. All rights reserved.Legal|Privacy policy|Modern Slavery Act Transparency Statement|Sitemap|About US| Contact US: help@patsnap.com