Method for modifying polarity of elastomer resin
A technology of elastomer resin and modification method, which is applied in the field of polar graft modification of elastomer resin melt, can solve the problems of dark color, poor thermoplasticity, unsuitable thermoplastic elastomer, etc., achieves high grafting rate, avoids The effect of over-crosslinking
- Summary
- Abstract
- Description
- Claims
- Application Information
AI Technical Summary
Problems solved by technology
Method used
Examples
Embodiment 1
[0013] Put 100 kg of natural rubber resin and 1 kg of sorbic acid into the internal mixer at one time, set the speed at 60 rpm, and mix the above-mentioned mixed raw materials evenly at 50°C to obtain a compound rubber material. The mixing time is 13 minutes to 14 minutes; Then the obtained composite rubber is sent to a flat vulcanizing machine, and the composite rubber is melted at 150° C., and the components inside the melt are kept to react for 30 minutes, discharged, and cooled to obtain a natural rubber resin grafted with sorbic acid.
[0014] After the resulting product was placed in vacuum at room temperature for 24 hours, a small amount of sample was extracted with dimethyl sulfoxide to remove the sorbic acid that did not participate in the grafting, and the extract was titrated with potassium hydroxide solution, and the grafting ratio of sorbic acid was measured and calculated. The branch rate is 100%; the polar modified natural rubber resin is heated and dissolved wit...
Embodiment 2
[0016] Put 75 kg of nitrile rubber containing 33% acrylonitrile and 1 kg of sorbic acid into the internal mixer at one time, set the speed at 60 rpm, and mix the above mixed raw materials evenly at 35°C to obtain a compound rubber. The time is 9 minutes to 10 minutes; then the obtained composite rubber is sent to a flat vulcanizer, and the composite rubber is formed into a melt at 195°C, and the components inside the melt are kept to react for 55 minutes, and the material is discharged and cooled to obtain sorbic acid grafting. Modified nitrile rubber resin.
[0017] After the resulting product was placed in vacuum at room temperature for 24 hours, a small amount of sample was extracted with dimethyl sulfoxide to remove the sorbic acid that did not participate in the grafting, and the extract was titrated with potassium hydroxide solution, and the grafting ratio of sorbic acid was measured and calculated. The branch rate is 98.76%; the polar modified nitrile rubber resin is he...
Embodiment 3
[0019] Put 100 kg of mixed resin mixed with natural rubber and styrene-butadiene rubber resin at a weight ratio of 1:9, 2.5 kg of sorbic acid, and set the rotor speed at 60 rpm to the internal mixer at 45 °C. Mix the above-mentioned mixed raw materials evenly to obtain a compound rubber material. The mixing time is 14 minutes to 15 minutes; then send the obtained compound rubber material into a twin-screw extruder, and set the temperature of each section of the extruder barrel: 135 in zone Ⅰ ℃±2, Zone Ⅱ 140℃±2, Zone Ⅲ 145℃±2, Zone Ⅳ 150℃±2, Zone Ⅴ 155℃±2, Zone Ⅵ 160℃, the die head temperature is 180℃±2, and the screw speed is controlled to Make the composite rubber material into a melt, keep the components in the melt to react for 14-15 minutes, and just extrude from the die head, and cool to obtain a natural rubber-styrene-butadiene rubber mixed resin grafted with sorbic acid.
[0020] After the resulting product was placed in vacuum at room temperature for 24 hours, a small ...
PUM
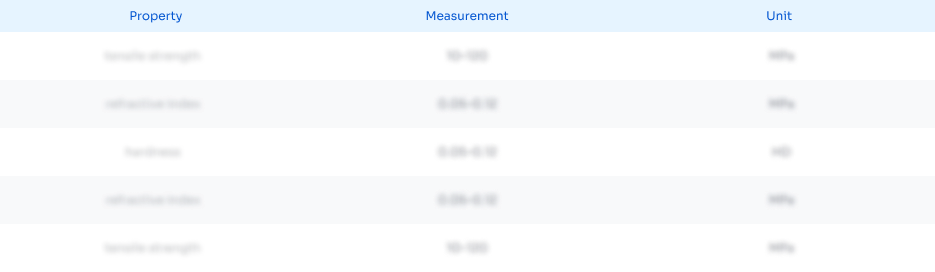
Abstract
Description
Claims
Application Information

- R&D
- Intellectual Property
- Life Sciences
- Materials
- Tech Scout
- Unparalleled Data Quality
- Higher Quality Content
- 60% Fewer Hallucinations
Browse by: Latest US Patents, China's latest patents, Technical Efficacy Thesaurus, Application Domain, Technology Topic, Popular Technical Reports.
© 2025 PatSnap. All rights reserved.Legal|Privacy policy|Modern Slavery Act Transparency Statement|Sitemap|About US| Contact US: help@patsnap.com