High-pressure roller milling-preselection processing method for vanadic titanomagnetite
A technology of vanadium-titanium magnetite and high-pressure roller milling, which is applied in chemical instruments and methods, magnetic separation, solid separation, etc., can solve the problems of low concentrate grade and recovery rate, and reduce grinding energy consumption and beneficiation efficiency Improve, improve the effect of a large range
- Summary
- Abstract
- Description
- Claims
- Application Information
AI Technical Summary
Problems solved by technology
Method used
Image
Examples
Embodiment 1
[0019] The original ore is vanadium-titanium magnetite in Panxi area, with a water content of 1% by mass, and an iron grade of 31.34% in the sample. TiO 2 The mass percentage is 12.46%, which is low-grade iron oxide ore, and its particle size composition is shown in Table 1.
[0020] The vanadium-titanium magnetite ore is superfinely crushed by a high-pressure roller mill and pre-selected and polished. The product after pre-selected and polished enters the ball mill classification closed circuit system. The process steps are as follows.
[0021] (1) After coarse crushing, medium crushing and fine crushing of raw ore, the particle size is below 12mm, and the high-pressure roller mill is used for ultra-fine crushing. The pressure between the rolls is 5MPa, the roll speed is 1.6m / min, and the roll gap is 5mm. The high-pressure roller mill ultra-fine crushing adopts an open-circuit crushing method: that is, the product after ultra-fine grinding of vanadium-titanium magnetite is directly...
Embodiment 2
[0033] The vanadium-titanium magnetite ore is superfinely crushed by a high-pressure roller mill and pre-selected and polished. The product after pre-selected and polished enters the ball mill classification closed circuit system. The process steps are as follows.
[0034] (1) After coarse crushing, medium crushing and fine crushing of raw ore, the particle size is below 12mm, and the high-pressure roller mill is used for ultra-fine crushing. The pressure between the rolls is 5MPa, the roll speed is 1.6m / min, and the roll gap is 5mm. The high-pressure roller mill ultra-fine crushing adopts the edge material circulation crushing method, and the proportion of the edge material circulation is 20%, 30% and 40% respectively according to the mass percentage; the particle size distribution of the high-pressure roller mill ultra-fine crushed product is shown in Table 4.
[0035] (2) Pre-selection
[0036] The ultra-fine crushed products of the high-pressure roller mill with a 30% side materi...
Embodiment 3
[0043] The vanadium-titanium magnetite ore is superfinely crushed by a high-pressure roller mill and pre-selected and polished. The product after pre-selected and polished enters the ball mill classification closed circuit system. The process steps are as follows.
[0044] (1) After coarse crushing, medium crushing and fine crushing of raw ore, the particle size is below 12mm, and the high-pressure roller mill is used for ultra-fine crushing. The pressure between the rolls is 5MPa, the roll speed is 1.6m / min, and the roll gap is 5mm. The ultra-fine crushing of the high-pressure roller mill adopts a fully closed-circuit crushing method: the product after the ultra-fine crushing of vanadium-titanium magnetite is sieved by a sieve with a mesh size of 3.5mm, and the product on the screen is returned to the high-pressure roller mill to be combined with the new feed ore and then crushed. The product under the sieve is fed into the next operation process.
[0045] (2) Pre-selection
[0046...
PUM
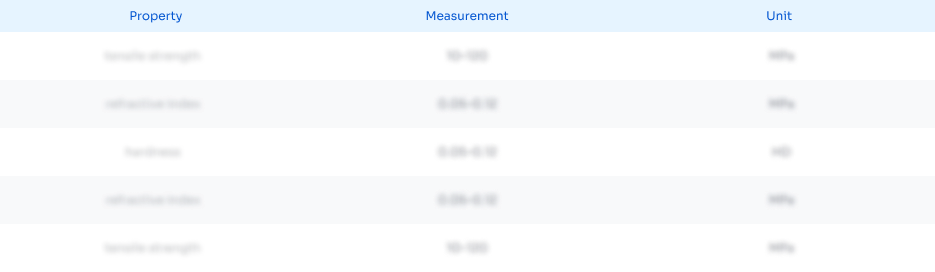
Abstract
Description
Claims
Application Information

- R&D
- Intellectual Property
- Life Sciences
- Materials
- Tech Scout
- Unparalleled Data Quality
- Higher Quality Content
- 60% Fewer Hallucinations
Browse by: Latest US Patents, China's latest patents, Technical Efficacy Thesaurus, Application Domain, Technology Topic, Popular Technical Reports.
© 2025 PatSnap. All rights reserved.Legal|Privacy policy|Modern Slavery Act Transparency Statement|Sitemap|About US| Contact US: help@patsnap.com