Shaking ladle premelting process for producing medium and low carbon ferromanganese
A low-carbon ferromanganese and process technology, which is applied in the shaking ladle pre-smelting process, can solve the problems of high desiliconization pressure, high heat loss, and high manganese ore consumption in the electric furnace of medium manganese refining, and achieve high desiliconization rate, low heat loss, The effect of shortening the smelting time
- Summary
- Abstract
- Description
- Claims
- Application Information
AI Technical Summary
Problems solved by technology
Method used
Examples
Embodiment 1
[0009] Select 17 tons of medium manganese shake slag with an alkalinity of 1.2 and a MnO content of 25% and 17 tons of hot manganese-silicon alloy and mix them into the shaker. The volume of the shaker is 15 m 3 , carry out the desiliconization reaction in the shaking bag, the number of revolutions of the shaking bag is 60 rpm, the shaking time is 20 minutes, and the manganese-silicon alloy is obtained after shaking, and the desiliconization amount is 5.96.
Embodiment 2
[0011] Select 18.5 tons of medium manganese shaking slag with an alkalinity of 1.3 and a MnO content of 20% and 15.5 tons of hot manganese silicon alloy and mix them into the shaking bag. The volume of the shaking bag is 15 m 3 , carry out the desiliconization reaction in the shaking bag, the rotation speed of the shaking bag is 50 rpm, the shaking time is 17 minutes, and the manganese-silicon alloy is obtained after shaking, and the desiliconization amount is 6.11.
Embodiment 3
[0013] Select medium manganese shake slag 17.8 with basicity of 1.2 and MnO content of 23% and hot manganese silicon alloy 16.2 to mix and put into the shaker, the volume of the shaker is 15 m 3 , carry out the desiliconization reaction in the shaking bag, the number of rotations of the shaking bag is 40 rpm, the shaking time is 15 minutes, and the manganese-silicon alloy is obtained after shaking, and the desiliconization amount is 6.01.
PUM
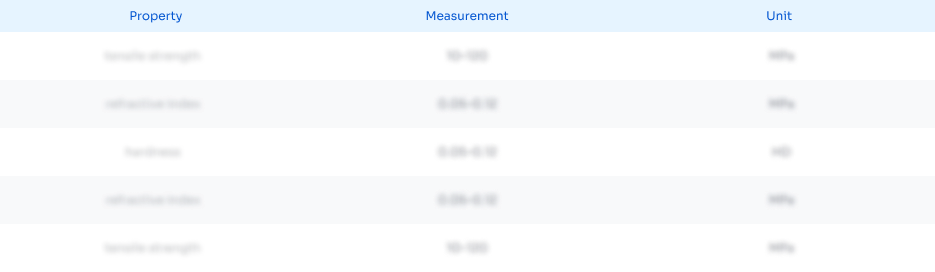
Abstract
Description
Claims
Application Information

- R&D Engineer
- R&D Manager
- IP Professional
- Industry Leading Data Capabilities
- Powerful AI technology
- Patent DNA Extraction
Browse by: Latest US Patents, China's latest patents, Technical Efficacy Thesaurus, Application Domain, Technology Topic, Popular Technical Reports.
© 2024 PatSnap. All rights reserved.Legal|Privacy policy|Modern Slavery Act Transparency Statement|Sitemap|About US| Contact US: help@patsnap.com