Welding method of solar energy battery plate
A technology of solar cells and welding methods, which is applied to high-frequency current welding equipment, welding equipment, metal processing equipment, etc., can solve the problems of low production efficiency and poor quality stability, and achieve high production efficiency, good welding quality, and shortened welding time. The effect of the time required for warm-up
- Summary
- Abstract
- Description
- Claims
- Application Information
AI Technical Summary
Problems solved by technology
Method used
Image
Examples
Embodiment Construction
[0016] The present invention will be further elaborated below in conjunction with accompanying drawing:
[0017] Such as figure 1 and figure 2 In the solar battery sheet welding method shown, first, the battery sheet 3 and the welding ribbon 2 are placed on the preheating plate 1, and the battery sheet 3 and the welding ribbon 2 are welded by heating the welding device, and the welding device includes a high-frequency generator 4. The metal rod 6 and the induction circuit 5 connecting the high-frequency generator 4 and the metal rod 6 , the induction circuit 5 is arranged around the metal rod 6 .
[0018] The induction loop 5 is composed of a plurality of helical coils and connecting wires, the helical coils are arranged around the metal rod 6, and the helical coils are wound at least once, and the number of turns of the helical coils can determine the size of the eddy current effect, The more coils are wound, the greater the eddy current effect will be, which can effective...
PUM
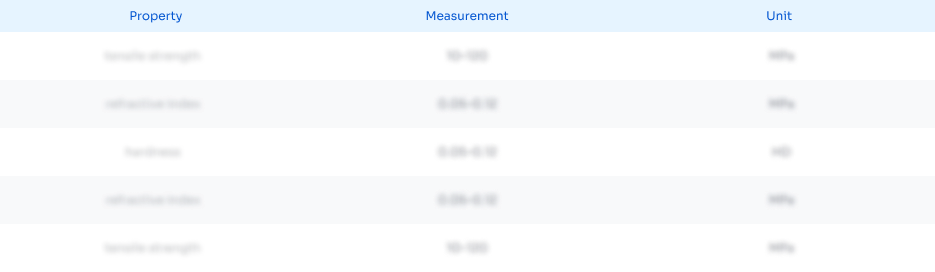
Abstract
Description
Claims
Application Information

- Generate Ideas
- Intellectual Property
- Life Sciences
- Materials
- Tech Scout
- Unparalleled Data Quality
- Higher Quality Content
- 60% Fewer Hallucinations
Browse by: Latest US Patents, China's latest patents, Technical Efficacy Thesaurus, Application Domain, Technology Topic, Popular Technical Reports.
© 2025 PatSnap. All rights reserved.Legal|Privacy policy|Modern Slavery Act Transparency Statement|Sitemap|About US| Contact US: help@patsnap.com