Method for reducing edge serration defects in thin slabs
A technology of serrated edges and thin slabs, applied in metal rolling and other directions, can solve problems such as productivity decline and steel damage, and achieve the effects of improving quality, increasing yield, improving reliability and productivity
- Summary
- Abstract
- Description
- Claims
- Application Information
AI Technical Summary
Problems solved by technology
Method used
Image
Examples
Embodiment
[0047] casting a thin slab containing niobium (Nb) and 0.20% to 0.28% by weight of carbon; then reheating in a heat treatment furnace so that the temperature of the thin slab output from the heat treatment furnace is 1040°C to 1090°C; Hot rolling is performed to prepare hot rolled coils.
[0048] From image 3 It can be seen that niobium carbide (NbC) begins to precipitate at a temperature of 1060 ° C to 1080 ° C; when the temperature of the thin slab output from the heat treatment furnace is equal to or higher than the precipitation temperature of niobium carbide (NbC), the edge jagged The defect index decreased rapidly.
[0049] In addition, when the temperature of the thin slab output from the heat treatment furnace is lower than 1060° C., niobium carbide (NbC) is precipitated rapidly, thus causing an increase in the edge serration index of the hot-rolled coil.
[0050] From Figure 4 It can be seen that although the microstructure of the thin slab varies with the temper...
PUM
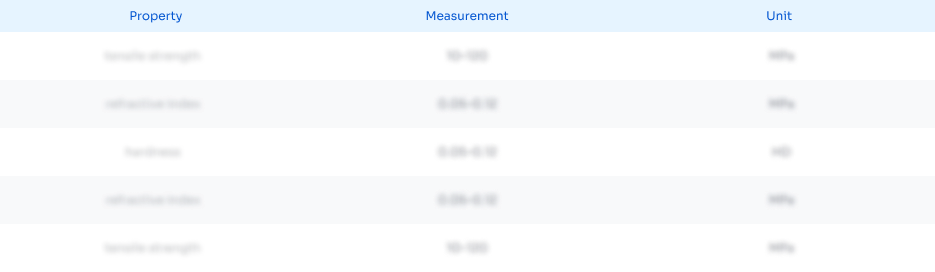
Abstract
Description
Claims
Application Information

- R&D Engineer
- R&D Manager
- IP Professional
- Industry Leading Data Capabilities
- Powerful AI technology
- Patent DNA Extraction
Browse by: Latest US Patents, China's latest patents, Technical Efficacy Thesaurus, Application Domain, Technology Topic, Popular Technical Reports.
© 2024 PatSnap. All rights reserved.Legal|Privacy policy|Modern Slavery Act Transparency Statement|Sitemap|About US| Contact US: help@patsnap.com