Device and method for preparing ethylbenzene by catalytic conversion of alcohol ether
A catalytic conversion, alcohol ether technology, applied in the chemical industry, to achieve the effect of easy re-aromatization, easy separation, and reduced settings
- Summary
- Abstract
- Description
- Claims
- Application Information
AI Technical Summary
Problems solved by technology
Method used
Image
Examples
Embodiment 1
[0020] The catalyst used was prepared by adding 0.5% lanthanum to a commercial aromatization catalyst. 100% conversion of methanol feedstock at 400°C, pressure 0.4 MPa (gauge pressure), in aromatization system 1 (using a fluidized bed reactor) under the condition that the weight space velocity of methanol is 0.3 g / gcat / h Produces the following products on a carbon-based mass basis: 3% methane and ethane, 12% ethylene, 24% C 3 -C 5 Hydrocarbons, 2% Benzene, 25% Toluene, Xylene and C 10 Aromatic hydrocarbons. After passing through the gas-liquid separation subsystem 3 and the gas-gas separation subsystem 4, the obtained C 3 -C 5 Hydrocarbons are recycled back to aromatization system 2 (using a fluidized bed reactor) at 550°C, pressure 0.4MPa (gauge pressure) and C 3 -C 5 The reaction was carried out under the condition that the weight space velocity of hydrocarbon was g / gcat / h, and the net conversion was 60%. Then the obtained product is brought into the gas-liquid separa...
Embodiment 2
[0022] The catalyst used was prepared by adding 1% lanthanum and 2% cerium to a commercial aromatization catalyst. Pure dimethyl ether was converted at 500° C. under a pressure of 0.1 MPa (gauge pressure), and under the condition that the weight space velocity of dimethyl ether was 12 g / gcat / h. The following products were produced in aromatization system 1 (using a fixed bed reactor) based on carbon-based mass: 3.5% methane and ethane, 12% ethylene, 30% C 3 -C 5 Hydrocarbons, 10% Benzene, 23% Toluene, Xylene and C 10 Aromatic hydrocarbons. After passing through the gas-liquid separation subsystem 3 and the gas-gas separation subsystem 4, the obtained C 3 -C 5Hydrocarbons are recycled back to aromatization system 2 (using a fixed bed reactor) at 700°C, pressure 0.1MPa (gauge pressure) and C 3 -C 5 The reaction was carried out under the condition of a weight space velocity of 10 g / gcat / h, and the net conversion rate was 70%. Then the obtained product is brought into the g...
Embodiment 3
[0024] A commercial aromatization Zn / ZSM-5 catalyst was added with 0.5% cerium to prepare the catalyst used to convert 50% dimethyl ether, 45% methanol and 5% water feedstock at 475°C, pressure 2MPa (gauge pressure), Under the condition that the weight space velocity of methanol is 30 g / gcat / h. In aromatization system 1 (using a fluidized bed reactor) the following products were produced on a carbon-based mass basis: 6% methane and ethane, 8% ethylene, 28% C 3 -C 5 Hydrocarbons, 10% Benzene, 23% Toluene, Xylene and C 10 Aromatic hydrocarbons. After passing through the gas-liquid separation subsystem 3 and the gas-gas separation subsystem 4, the obtained C 3 -C 5 Hydrocarbons are recycled back to aromatization system 2 (using a fluidized bed reactor) at 600°C, pressure 2MPa (gauge pressure) and C 3 -C 5 The reaction was carried out at a weight space velocity of hydrocarbons of 7 g / gcat / h with a net conversion of 69%. Then the obtained product is brought into the gas-liqu...
PUM
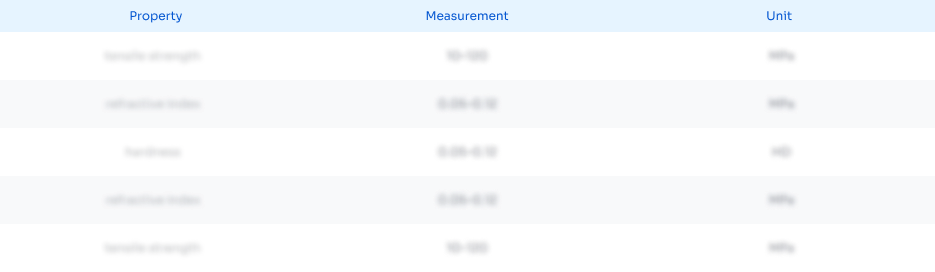
Abstract
Description
Claims
Application Information

- R&D
- Intellectual Property
- Life Sciences
- Materials
- Tech Scout
- Unparalleled Data Quality
- Higher Quality Content
- 60% Fewer Hallucinations
Browse by: Latest US Patents, China's latest patents, Technical Efficacy Thesaurus, Application Domain, Technology Topic, Popular Technical Reports.
© 2025 PatSnap. All rights reserved.Legal|Privacy policy|Modern Slavery Act Transparency Statement|Sitemap|About US| Contact US: help@patsnap.com