Micro-foaming injection-molding screw rod
An injection molding and micro-foaming technology, applied in the field of injection molding screws, can solve problems such as insufficient mixing capacity, and achieve the effects of increasing conveying capacity and shearing capacity, relieving pressure increase, and improving mixing effect.
- Summary
- Abstract
- Description
- Claims
- Application Information
AI Technical Summary
Problems solved by technology
Method used
Image
Examples
Embodiment Construction
[0018] A microfoaming injection molding screw, such as figure 1 As shown, it mainly consists of rear screw 1, rear positioning ring 2, rear check ring 3, rear mixing section 4, front mixing section 5, front screw 6, front positioning ring 7, front check ring 8 and screw head 9 Composition; the tail of the rear screw 1 has a keyway, which is installed on the injection machine through the keyway and the key; the head of the rear screw 1 has a threaded hole, and the tail of the rear mixing section 4 has a rear stepped shaft 11, and the rear stepped shaft 11 The end has a rear stepped shaft thread 12, the rear positioning ring 2 and the rear check ring 3 are sequentially set on the rear stepped shaft 11 of the rear mixing section 4, and the rear mixing section 4 is connected to the rear screw 1 through the rear stepped shaft 11 The head of the rear mixing section 4 has a front stepped shaft 14, the end of the front stepped shaft 14 has a front stepped shaft thread 15, the tail of ...
PUM
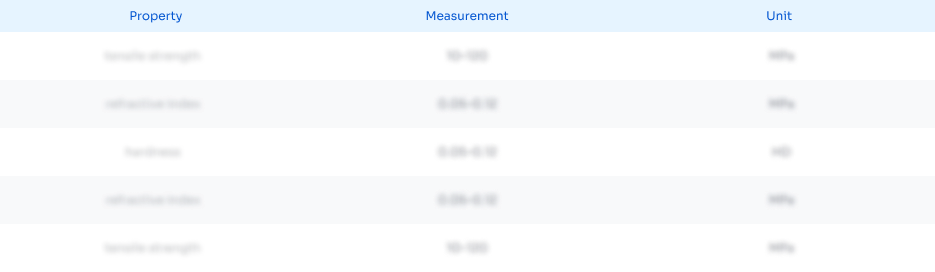
Abstract
Description
Claims
Application Information

- R&D
- Intellectual Property
- Life Sciences
- Materials
- Tech Scout
- Unparalleled Data Quality
- Higher Quality Content
- 60% Fewer Hallucinations
Browse by: Latest US Patents, China's latest patents, Technical Efficacy Thesaurus, Application Domain, Technology Topic, Popular Technical Reports.
© 2025 PatSnap. All rights reserved.Legal|Privacy policy|Modern Slavery Act Transparency Statement|Sitemap|About US| Contact US: help@patsnap.com