Full-counterflow heat exchange two-section type casting waste sand roasting furnace
A kind of casting waste sand, two-stage technology, which is applied in casting molding equipment, manufacturing tools, machinery for cleaning/processing of casting materials, etc. Stability and other issues, to achieve high production efficiency, beneficial to resources and environmental protection, and good quality.
- Summary
- Abstract
- Description
- Claims
- Application Information
AI Technical Summary
Problems solved by technology
Method used
Image
Examples
Embodiment 1
[0025] Embodiment one: see figure 1 , figure 2 and Image 6 A full countercurrent heat exchange two-stage casting waste sand roasting furnace is shown, comprising an upper furnace body 3 positioned and connected to a steel frame 4, a lower furnace body 6 positioned and connected to a base 10, and a furnace body 6 positioned on the top of the upper furnace body. The exhaust port 2, the sand adding device 21 and the sand adding pipe 1, the sand collection bucket 22 arranged at the junction of the upper furnace body and the lower furnace body, the three burners 18 arranged on the upper part of the lower furnace body, and the lower furnace body The three burners 7 in the upper part of the body, the air inlet 17 arranged at the lower part of the lower furnace body, the lower sand collection bucket 13 arranged at the bottom of the lower furnace body and the sand feeding cooling pipe 16 and the sand outlet 14 connected thereto;
[0026] A pneumatic sand separator 20 is set in the ...
Embodiment 2
[0033] Embodiment two: see image 3 The furnace walls of the upper furnace body 3 and the lower furnace body 6 of this example are all made of steel plates, heat-insulating fibers, and heat-resistant stainless steel plates from the outside to the inside. The diameter of the upper furnace body 3 is equal to the diameter of the lower furnace body 6. The upper furnace body The furnace body and the lower furnace body are directly connected as one, and temperature sensors 24 are respectively arranged on the upper furnace body and the lower furnace body, and the rest are the same as in the first embodiment. The furnace body with such a structure has good heat insulation and heat preservation performance and long service life, which is beneficial to improve the utilization rate of heat energy in the furnace and realize maintenance-free.
[0034]When the present invention works, foundry waste sand is added from the sand feeding pipe in the upper section of the furnace body with a cert...
PUM
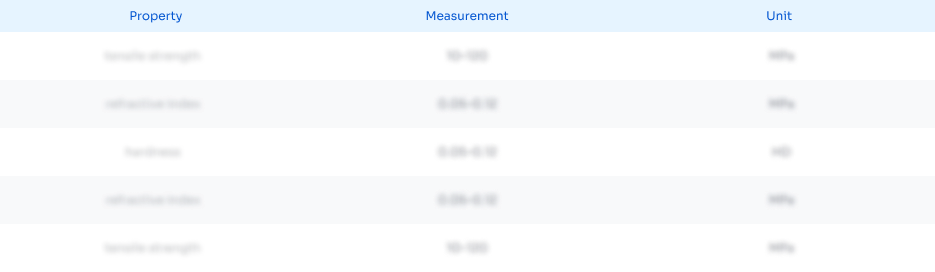
Abstract
Description
Claims
Application Information

- Generate Ideas
- Intellectual Property
- Life Sciences
- Materials
- Tech Scout
- Unparalleled Data Quality
- Higher Quality Content
- 60% Fewer Hallucinations
Browse by: Latest US Patents, China's latest patents, Technical Efficacy Thesaurus, Application Domain, Technology Topic, Popular Technical Reports.
© 2025 PatSnap. All rights reserved.Legal|Privacy policy|Modern Slavery Act Transparency Statement|Sitemap|About US| Contact US: help@patsnap.com