Method for producing marble art paper
A production method and art paper technology, applied in special paper, paper, papermaking and other directions, to achieve the effects of reliable production process, prevention of eye fatigue, good artistic sense and aesthetic sense
- Summary
- Abstract
- Description
- Claims
- Application Information
AI Technical Summary
Problems solved by technology
Method used
Examples
Embodiment 1
[0013] Embodiment 1: A kind of preparation method of marble art paper, the slurry proportioning that selects is 20% of Canadian Kelly Pu coniferous wood pulp, 80% of Rizhao Senbo hardwood pulp, the slurry beating adopts the mode of mixed beating, and the pulp is controlled The beating degree of material beating is 34°SR, the concentration of slurry on the Internet is 0.9-1.0%, and the surface absorption weight is 20-30g / m 2 , Surface sizing: AKD dosage is 1.0% (mass ratio of AKD stock solution to absolute dry pulp). Paper machine production speed: 50m / min. Paper weight: 95g / m 2 .
[0014] The paper is dyed twice in two stages. In the first dyeing, the dye is added at the head box of the paper machine, and the dye is directly added into the head box with liquid dye and mixed with the pulp, and the paper pulp forms a single-color background color. Dye dosage for one dyeing: Clariant liquid dye yellow 602ppm (liquid dye stock solution relative to dry pulp quality, the same bel...
Embodiment 2
[0015] Embodiment 2: A kind of preparation method of marble art paper, the slurry proportioning of selection is 20% of Canadian Kelly Pu coniferous wood pulp, 80% of Rizhao Senbo hardwood pulp, the slurry beating adopts the mode of mixed beating, control pulp The beating degree of material beating is 35°SR, the concentration of slurry on the Internet is 1.0%, and the surface absorption weight is 20-25g / m 2 , Surface sizing: AKD dosage is 1.0% (mass ratio of AKD stock solution to absolute dry pulp). Paper machine production speed: 50m / min. Paper weight: 95g / m 2 .
[0016] The paper is dyed twice in two stages. In the first dyeing, the dye is added at the head box of the paper machine, and the dye is directly added into the head box with liquid dye and mixed with the pulp, and the paper pulp forms a single-color background color. Dye dosage for one-time dyeing: Clariant liquid dye yellow 25ppm (liquid dye stock solution relative to dry pulp quality, the same below), Clariant ...
PUM
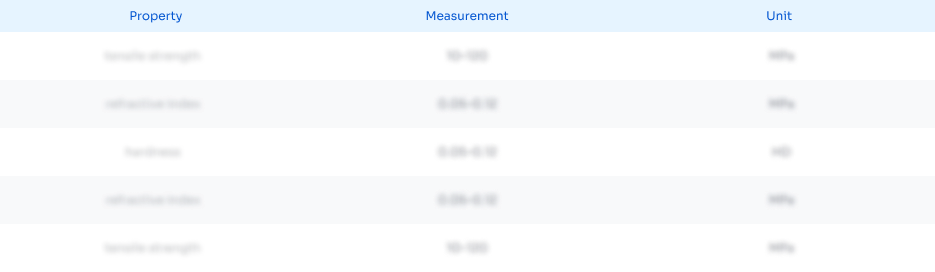
Abstract
Description
Claims
Application Information

- R&D
- Intellectual Property
- Life Sciences
- Materials
- Tech Scout
- Unparalleled Data Quality
- Higher Quality Content
- 60% Fewer Hallucinations
Browse by: Latest US Patents, China's latest patents, Technical Efficacy Thesaurus, Application Domain, Technology Topic, Popular Technical Reports.
© 2025 PatSnap. All rights reserved.Legal|Privacy policy|Modern Slavery Act Transparency Statement|Sitemap|About US| Contact US: help@patsnap.com