Technological method for producing high-purity low-iron aluminum sulfate by using coal ash and comprehensively utilizing coal ash
A low-iron aluminum sulfate and process method technology, applied in aluminum sulfate, cement production, aluminum-sulfur compounds and other directions, can solve the problems of high impurity content in aluminum sulfate products, many aluminum sulfate crystals, product use restrictions, etc., and achieve comprehensive utilization benefits. Significant, low-cost effects
- Summary
- Abstract
- Description
- Claims
- Application Information
AI Technical Summary
Problems solved by technology
Method used
Image
Examples
Embodiment 1
[0039] Embodiment 1: raw material fly ash is composed of: Al 2 o3 Content 37.7%, Fe 2 o 3 Content 4.38%, CaO content 3.74%, MgO content 0.54%, SiO 2 The content is 49.9%, and the loss on ignition is 1.92%. The raw fly ash can also use other components and their corresponding amounts.
[0040] Mill the fly ash in a ball mill for 1 hour to perform mechanical activation; add water according to the mass ratio of fly ash to water of 1:3, fully stir, remove unburned black through flotation; and remove iron oxide through magnetic separation; The fly ash residue after flotation carbon and magnetic separation of iron and concentrated sulfuric acid are made into a mixed solution with a sulfuric acid concentration of 40%. The solid-liquid ratio of the fly ash and the mixed solution is controlled to be 1:8. Heating and pressurizing the reaction for 3 hours, the highest temperature of the reaction is 240 °C; after the reaction cools down, add water according to the mass ratio of fly as...
Embodiment 2
[0044] Embodiment 2: with the fly ash in embodiment 1, ball mill 2h in ball mill, carry out mechanical activation; According to the mass ratio of fly ash and water is 1: 3, add water, fully stir, remove unburned net through flotation black; then remove the iron oxide by magnetic separation; make a mixed solution with a sulfuric acid concentration of 50% from the fly ash residue after the flotation of carbon and magnetic iron with concentrated sulfuric acid, and control the solid-liquid mixture of the fly ash and the mixed solution The ratio is 1:7, heat and pressurize the reaction for 4 hours in the acid-resistant reaction equipment, the highest temperature of the reaction is 240 ° C; The filter cake was obtained by filtration, and washed with water with a mass ratio of fly ash to water of 1:1 to obtain a crude aluminum sulfate solution. The extraction rate of aluminum analyzed was 75%.
[0045] Evaporate and concentrate the crude aluminum sulfate solution at 110°C to 1 / 10 of...
Embodiment 3
[0047] Embodiment 3: with the fly ash in embodiment 1, ball mill 3h in ball mill, carry out mechanical activation; According to the mass ratio of fly ash and water is 1: 2, add water, fully stir, remove unburned net through flotation black; and then remove iron oxide by magnetic separation; make a mixed solution with a sulfuric acid concentration of 80% from the fly ash residue after flotation carbon and magnetic iron separation and concentrated sulfuric acid, and control the solid-liquid concentration of fly ash and the mixed solution Ratio of 1:6, heating and pressurizing reaction in acid-resistant reaction equipment for 5h, the highest temperature of the reaction is 240°C; The filter cake was obtained by filtration, and washed with water with a mass ratio of fly ash to water of 1:2 to obtain a crude aluminum sulfate solution. The extraction rate of aluminum analyzed was 72%.
[0048] Evaporate and concentrate the aluminum sulfate crude liquid at 100°C to 1 / 10 of the origin...
PUM
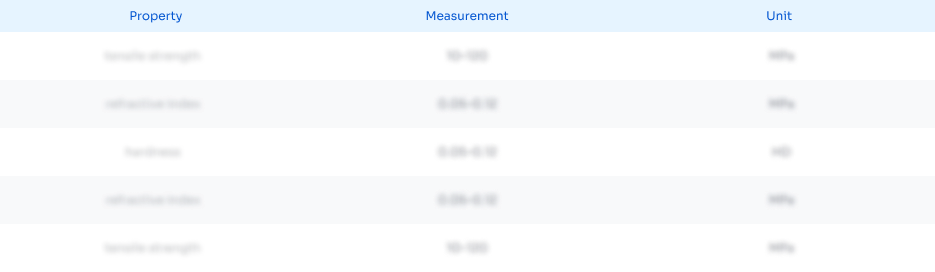
Abstract
Description
Claims
Application Information

- Generate Ideas
- Intellectual Property
- Life Sciences
- Materials
- Tech Scout
- Unparalleled Data Quality
- Higher Quality Content
- 60% Fewer Hallucinations
Browse by: Latest US Patents, China's latest patents, Technical Efficacy Thesaurus, Application Domain, Technology Topic, Popular Technical Reports.
© 2025 PatSnap. All rights reserved.Legal|Privacy policy|Modern Slavery Act Transparency Statement|Sitemap|About US| Contact US: help@patsnap.com