Composite boiler and production method thereof
A composite pot and magnetic conductive metal technology, applied in chemical instruments and methods, layered products, metal layered products, etc., can solve problems such as easy falling off and affect heat conduction efficiency, achieve large magnetic conductive heat generation area, and improve efficiency. , the effect of reducing the number of
- Summary
- Abstract
- Description
- Claims
- Application Information
AI Technical Summary
Problems solved by technology
Method used
Image
Examples
Embodiment Construction
[0033] Attached below Figures 1 to 8 The preferred embodiments for implementing the present invention will be further described. This embodiment is a composite pot that can be used in an induction cooker. The magnetic metal bottom plate is made of stainless iron sheet or ordinary metal iron sheet, and aluminum material is used as the metal base material.
[0034] In the figure, 1 is the cavity, 2 is the bottom of the pot, 3 is the magnetic metal bottom plate, 4 is the metal substrate, 5 is the limit column, 6 is the rear mold of the die-casting mold, 7 is the front mold of the die-casting mold, and 8 is the casting Mouth, 30 is a groove, 31 is a fracture surface, 32 is a groove bottom wall, 33 is a groove upper wall, 34 is a non-fracture side wall of a groove, 35 is a limiting post hole, and 40 is a gap.
[0035] figure 1 It is the front view of the compound pot implementing the preferred embodiment of the present invention, and it is also figure 2 A-A sectional view in, ...
PUM
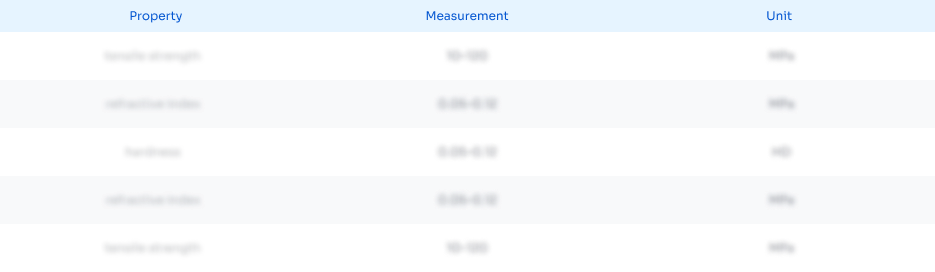
Abstract
Description
Claims
Application Information

- R&D
- Intellectual Property
- Life Sciences
- Materials
- Tech Scout
- Unparalleled Data Quality
- Higher Quality Content
- 60% Fewer Hallucinations
Browse by: Latest US Patents, China's latest patents, Technical Efficacy Thesaurus, Application Domain, Technology Topic, Popular Technical Reports.
© 2025 PatSnap. All rights reserved.Legal|Privacy policy|Modern Slavery Act Transparency Statement|Sitemap|About US| Contact US: help@patsnap.com