Method for preparing propylene from refinery mixed C4
A technology of mixing C4 and propylene, which is applied in the direction of hydrocarbon cracking to hydrocarbon, sustainable manufacturing/processing, only multi-stage series refining and cracking process treatment, etc. Low efficiency and other problems, to achieve the effect of reducing ineffective materials, good technical effects, investment and operating costs
- Summary
- Abstract
- Description
- Claims
- Application Information
AI Technical Summary
Problems solved by technology
Method used
Image
Examples
Embodiment 1
[0038] according to figure 1 As shown, the mixed carbon four composition (weight %) after etherification in the refinery is: isobutane: 40%, n-butane: 15%, butene-1: 17%, butene-2: 28%. The hydroisomerization catalyst used in catalytic distillation is metallic nickel supported on alumina. The catalytic cracking reactor adopts a fixed bed, and the catalyst loaded is a ZSM-5 molecular sieve catalyst. The reaction temperature is preferably 510° C., and the reaction pressure is preferably 0.18 MPa. Unreacted C recycled to catalytic cracking reactor 4 The proportion is 95% (volume), recycled to the C of the catalytic cracking reactor 2 - The proportion of fractions is 95% (volume), and the experiment proves that the propylene product obtained by adopting the device of the present invention to process 100,000 tons of mixed carbon four scale annually is 20,000 tons / year.
Embodiment 2
[0040] according to figure 1 As shown, the mixed carbon four composition (weight %) after etherification in the refinery is: isobutane: 40%, n-butane: 15%, butene-1: 17%, butene-2: 28%. The hydroisomerization catalyst used in the catalytic distillation is aluminum oxide supported metal palladium and zinc. The catalytic cracking reactor adopts a fluidized bed, and the catalyst loaded is a SAPO-34 molecular sieve catalyst. The reaction temperature is preferably 460° C., and the reaction pressure is preferably 0.25 MPa. Unreacted C recycled to catalytic cracking reactor 4 The proportion is 80% (volume), recycled to the C of the catalytic cracking reactor 2 - The proportion of the fraction is 80% (volume), and the experiment proves that the propylene product obtained by adopting the device of the present invention to process 100,000 tons of mixed carbon four scale is 18,000 tons / year.
Embodiment 3
[0042] according to figure 1 As shown, the mixed carbon four composition (weight %) after etherification in the refinery is: isobutane: 40%, n-butane: 15%, butene-1: 17%, butene-2: 28%. The hydroisomerization catalyst used in catalytic distillation is metallic nickel supported on alumina. The catalytic cracking reactor adopts a fixed bed, and the catalyst loaded is a ZSM-5 molecular sieve catalyst. The reaction temperature is preferably 460° C., and the reaction pressure is preferably 0.1 MPa. Unreacted C recycled to catalytic cracking reactor 4 The proportion is 66% (volume), recycled to the C of the catalytic cracking reactor 2 - The proportion of fractions is 85% (volume), and the experiment proves that the propylene product obtained by adopting the device of the present invention to process 100,000 tons of mixed carbon four scale is 17,000 tons / year.
PUM
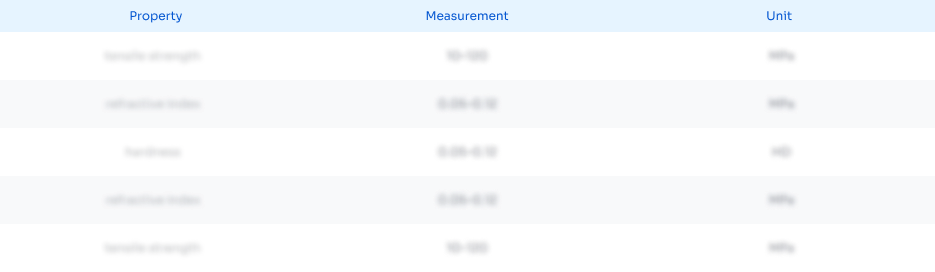
Abstract
Description
Claims
Application Information

- Generate Ideas
- Intellectual Property
- Life Sciences
- Materials
- Tech Scout
- Unparalleled Data Quality
- Higher Quality Content
- 60% Fewer Hallucinations
Browse by: Latest US Patents, China's latest patents, Technical Efficacy Thesaurus, Application Domain, Technology Topic, Popular Technical Reports.
© 2025 PatSnap. All rights reserved.Legal|Privacy policy|Modern Slavery Act Transparency Statement|Sitemap|About US| Contact US: help@patsnap.com