Method for manufacturing polyethylene microporous filter tube for secondary filtering of compressed air
A technology of precision filtration and compressed air, which is applied in separation methods, dispersed particle filtration, chemical instruments and methods, etc. It can solve the problems that the filter element cannot be formed at one time, waste of resources, and generation of rusty water, etc., to achieve better filtration effect and longer service life. Extended and stable filtration accuracy
- Summary
- Abstract
- Description
- Claims
- Application Information
AI Technical Summary
Problems solved by technology
Method used
Examples
Embodiment Construction
[0027] The polyethylene powder with a molecular weight of 4 million units is used as a raw material.
[0028] A. Sieve the polyethylene powder with a sifter.
[0029] B. The length of the mold body is 1m, and the inner diameter of the outer iron pipe mold is 50mm. Apply silicone oil to the inner wall of the outer iron pipe mold and the outer wall of the inner iron pipe mold for pouring sintering, and assemble the mold body, the inner wall of the outer iron pipe mold and the inner iron pipe mold The spacing between the outer walls is 9 mm.
[0030] C. Take the sieved material sifted by the powder sieving machine and pour it between the inner wall of the outer iron pipe mold and the outer wall of the inner iron pipe mold of the mold body, and pour it while vibrating.
[0031] D. Put the mold body into a constant temperature furnace and sinter at 280°C for 6 hours.
[0032] E. The mold body is released from the oven and cooled to room temperature.
[0033] The resulting filter...
PUM
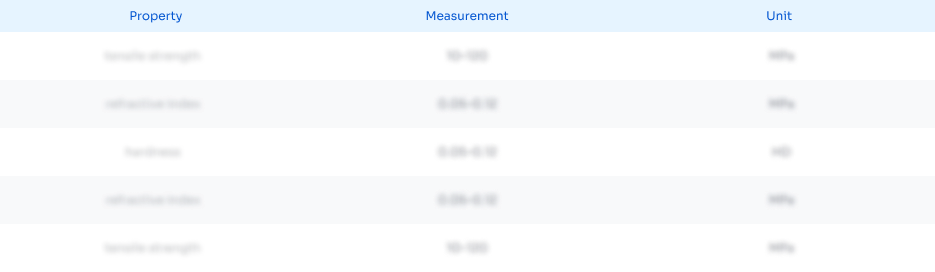
Abstract
Description
Claims
Application Information

- R&D
- Intellectual Property
- Life Sciences
- Materials
- Tech Scout
- Unparalleled Data Quality
- Higher Quality Content
- 60% Fewer Hallucinations
Browse by: Latest US Patents, China's latest patents, Technical Efficacy Thesaurus, Application Domain, Technology Topic, Popular Technical Reports.
© 2025 PatSnap. All rights reserved.Legal|Privacy policy|Modern Slavery Act Transparency Statement|Sitemap|About US| Contact US: help@patsnap.com