Method for preparing methyl levulinate by utilizing plant straws
A technology of methyl levulinate and plant straw, which is applied in the field of preparation of methyl levulinate, which can solve the problems of woody residue reuse restrictions, corrosion and environmental pollution, and inability to separate woody residue, and achieve process conditions that are easy to control , The equipment is less corrosive and the product quality is stable
- Summary
- Abstract
- Description
- Claims
- Application Information
AI Technical Summary
Problems solved by technology
Method used
Image
Examples
Embodiment 1
[0047] 1. Preparation of raw materials:
[0048] Crushing wheat stalks with a water content of 15% into 5-10mm straw fragments for later use;
[0049] 2. Acid hydrolysis
[0050] Mix the wheat straw fragments with the heavy superphosphate solution and stir evenly to form a straw slurry, wherein the mass percent concentration of the heavy superphosphate solution is 5%, and the weight ratio of the straw fragments to the heavy superphosphate solution is 1:0.3 ;
[0051] The straw pulp is pressed into the first reactor with a high-pressure screw pump, and at the same time, high-pressure steam is introduced into the first reactor to increase the temperature and pressure in the first reactor, and the first stage of acid hydrolysis treatment is carried out. Obtain the first acid hydrolysis mixture, wherein, the temperature of the high-pressure steam is 230°C, the absolute pressure is 2.6MPa, the acid hydrolysis treatment temperature of the first stage is controlled to be 230°C, the...
Embodiment 2
[0073] 1. Preparation of raw materials:
[0074] The sunflower seed shells with a water content of 5% are crushed into 1-3mm sunflower shell fragments for later use;
[0075] 2. Acid hydrolysis
[0076] Mix sunflower husk fragments with heavy superphosphate solution, stir evenly to form straw slurry, wherein the mass percent concentration of heavy superphosphate solution is 8%, and the weight ratio of straw fragments to heavy superphosphate solution is 1: 0.1;
[0077] The straw pulp is pressed into the first reactor with a high-pressure screw pump, and at the same time, high-pressure steam is introduced into the first reactor to increase the temperature and pressure in the first reactor, and the first stage of acid hydrolysis treatment is carried out. Obtain the first acid hydrolysis mixture, wherein the temperature of the high-pressure steam is 240°C, the absolute pressure is 3.1MPa, the pressure treatment temperature is controlled to be 235°C, the absolute pressure is 3.0...
Embodiment 3
[0095] 1. Preparation of raw materials:
[0096] The reed stalks with a water content of 10% are crushed into straw fragments of 3-5 mm for later use;
[0097] 2. Acid hydrolysis
[0098] Mix reed stalk fragments with heavy superphosphate solution, stir evenly to form straw pulp, wherein the mass percent concentration of heavy superphosphate solution is 6.5%, and the weight ratio of straw fragments to heavy superphosphate solution is 1:0.2 ;
[0099] The straw pulp is pressed into the first reactor with a high-pressure screw pump, and at the same time, high-pressure steam is introduced into the first reactor to increase the temperature and pressure in the first reactor, and the first stage of acid hydrolysis treatment is carried out. Obtain the first acid hydrolysis mixture, wherein the temperature of the high-pressure steam is 245°C, the absolute pressure is 2.2MPa, the acid hydrolysis treatment temperature of the first stage is controlled to be 240°C, the absolute pressure...
PUM
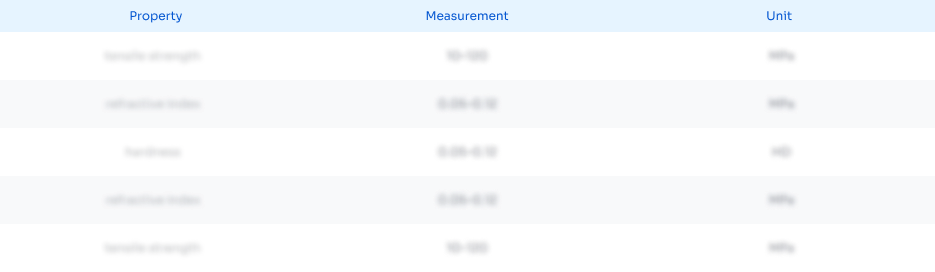
Abstract
Description
Claims
Application Information

- R&D
- Intellectual Property
- Life Sciences
- Materials
- Tech Scout
- Unparalleled Data Quality
- Higher Quality Content
- 60% Fewer Hallucinations
Browse by: Latest US Patents, China's latest patents, Technical Efficacy Thesaurus, Application Domain, Technology Topic, Popular Technical Reports.
© 2025 PatSnap. All rights reserved.Legal|Privacy policy|Modern Slavery Act Transparency Statement|Sitemap|About US| Contact US: help@patsnap.com