Method for producing iron foil by carbonylation
A technology of carbonylation and carbonyl iron, applied in the field of metallurgy, can solve the problems of high cost, heavy pollution, and high cost of steel rolling, and achieve the effects of not being easy to oxidize and spontaneously combust, reduce production costs, and simplify the process flow
- Summary
- Abstract
- Description
- Claims
- Application Information
AI Technical Summary
Problems solved by technology
Method used
Examples
Embodiment 1
[0024] Put 1Kg of hydrogen-activated sponge iron with 95% iron content in the synthesis kettle, and pass in CO gas with a purity of not less than 99.9%, control the pressure in the synthesis kettle to 9Mpa, and the temperature to 240°C. Sponge iron and carbon monoxide The gas undergoes selective carbonylation reaction in the synthesis kettle for 32 hours to generate carbonyl iron gas; the temperature in the synthesis kettle is naturally cooled to 40-25°C, the carbonyl iron gas decomposes to form iron foil, and nitrogen gas with a pressure of 0.3Mpa is introduced into the In the synthesis kettle, replace and remove the undecomposed carbonyl iron gas in the synthesis kettle to obtain iron foil. The size of the iron foil is 5-50mm×5-50mm×0.2-0.25mm, the weight is 0.74Kg, and the purity is 98.0%. Its surface is dense and smooth, and its thickness is uniform.
Embodiment 2
[0026] Put 1Kg of hydrogen-activated sponge iron with 97% iron content in the synthesis kettle, and feed CO gas with a purity of not less than 99.9%, control the pressure in the synthesis kettle to 15Mpa, and the temperature to 150°C. The sponge iron and carbon monoxide The gas undergoes selective carbonylation reaction in the synthesis kettle for 50 hours to generate carbonyl iron gas, and the temperature in the synthesis kettle is naturally cooled to 40-25°C, the carbonyl iron gas decomposes to form iron foil, and nitrogen gas with a pressure of 0.7Mpa is introduced into the In the synthesis kettle, replace and remove the undecomposed carbonyl iron gas in the synthesis kettle to obtain iron foil. The size of the iron foil is 5-50mm×5-50mm×0.15-0.2mm, the weight is 0.71Kg, the purity is 98.0%, the surface is dense and smooth, and the thickness is uniform.
Embodiment 3
[0028] Put 1Kg of hydrogen-activated sponge iron with 96% iron content in the synthesis kettle, and feed CO gas with a purity of not less than 99.9%, control the pressure of the synthesis kettle to 12Mpa, and the temperature to 195°C, and the sponge iron and carbon monoxide gas are synthesized Selective carbonylation reaction occurred in the kettle for 41 hours to generate carbonyl iron gas. The temperature in the synthesis kettle was naturally cooled to 40-25°C. The carbonyl iron gas was decomposed to form iron foil, and nitrogen gas with a pressure of 0.5Mpa was introduced into the synthetic In the kettle, replace and remove the undecomposed carbonyl iron gas in the synthesis kettle to obtain iron foil. The size of the iron foil is 5-50mm×5-50mm×0.1-0.15mm, the weight is 0.65Kg, the purity is 98.0%, the surface is dense and smooth, and the thickness is uniform.
PUM
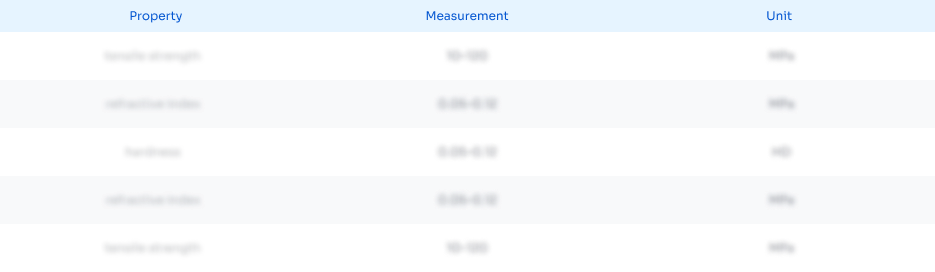
Abstract
Description
Claims
Application Information

- R&D Engineer
- R&D Manager
- IP Professional
- Industry Leading Data Capabilities
- Powerful AI technology
- Patent DNA Extraction
Browse by: Latest US Patents, China's latest patents, Technical Efficacy Thesaurus, Application Domain, Technology Topic, Popular Technical Reports.
© 2024 PatSnap. All rights reserved.Legal|Privacy policy|Modern Slavery Act Transparency Statement|Sitemap|About US| Contact US: help@patsnap.com