Method for preparing polished crystal tile
A technique of polishing crystal bricks and brick surfaces, which is applied in the field of preparation of polished crystal bricks, can solve problems such as poor exhaust effect, narrow melting temperature, and many glazed bubbles, and achieve less bubbles, high transparency, and good glaze quality Effect
- Summary
- Abstract
- Description
- Claims
- Application Information
AI Technical Summary
Problems solved by technology
Method used
Examples
preparation example Construction
[0013] The invention discloses a method for preparing polished crystal tiles, which comprises depositing a mixture of low-temperature frit and high-temperature frit on the surface of printed tiles fired at high temperature, and then undergoing low-temperature secondary firing and polishing to obtain products.
[0014] Preferably, the composition of the low temperature frit is: Al 2 o 3 5-7 parts, SiO 2 62~68 parts, CaO 2~6 parts, MgO 0~2 parts, K 2 O 3~6 parts, Na 2 O 2~5 parts, B 2 o 3 9-16 parts, 3-7 parts of BaO, the said parts are parts by mass, and its melting temperature is between 950-1050°C.
[0015] Preferably, the composition of the high-temperature frit is: Al 2 o 3 6-11 parts, SiO 2 54~64 parts, CaO 4~10 parts, K 2 O 1~4 parts, Na 2 O 1~3 parts, B 2 o 3 3-8 parts, MgO 0-2 parts, ZnO 4-10 parts, BaO 3-7 parts, the melting temperature is between 1000-1150 °C.
[0016] By using this specific low-temperature frit and high-temperature frit together, b...
Embodiment 1
[0024] Mix the 20-200 mesh low-temperature frit and high-temperature frit at a ratio of 100:10, pile them on the surface of the high-temperature fired printed bricks, the pile thickness is 4mm, fire at 950°C, and polish. Among them, the composition of the low-temperature frit is: Al 2 o 3 5 parts, SiO 2 62 parts, CaO 2 parts, K 2 O 6 parts, Na 2 O 3 parts, BaO 3 parts, B 2 o 3 15 parts; the composition of the high-temperature frit is: Al 2 o 3 6 parts, SiO 2 64 parts, CaO 8 parts, K 2 O 4 parts, Na 2 O 2 parts, B 2 o 3 4 parts, ZnO 4 parts, BaO 3 parts.
Embodiment 2
[0026] Mix the 20-120 mesh low-temperature frit and high-temperature frit at a ratio of 100:40, pile them on the surface of the high-temperature fired printed bricks, the pile thickness is 3.5mm, fire at 1000°C, and polish. Among them, the composition of the low-temperature frit is: Al 2 o 3 6 parts, SiO 2 68 parts, 4 parts of CaO, 1 part of MgO, K 2 O 5 parts, Na 2 O 4 parts, BaO 5 parts, B 2 o 3 10 parts; the composition of the high-temperature frit is: Al 2 o 3 9 parts, SiO 2 54 parts, CaO 6 parts, K 2 O 3 parts, Na 2 O 3 parts, B 2 o 3 3 parts, MgO 2 parts, ZnO 8 parts, BaO 7 parts.
PUM
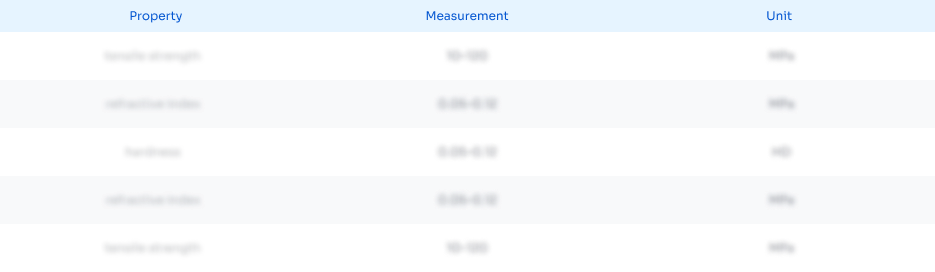
Abstract
Description
Claims
Application Information

- R&D
- Intellectual Property
- Life Sciences
- Materials
- Tech Scout
- Unparalleled Data Quality
- Higher Quality Content
- 60% Fewer Hallucinations
Browse by: Latest US Patents, China's latest patents, Technical Efficacy Thesaurus, Application Domain, Technology Topic, Popular Technical Reports.
© 2025 PatSnap. All rights reserved.Legal|Privacy policy|Modern Slavery Act Transparency Statement|Sitemap|About US| Contact US: help@patsnap.com