Method for preparing polyester, polyether and modified silicone oil ternary copolymer textile finishing agent
A technology of silicone oil ternary copolymerization fabric and polyether modified silicone oil, which is applied in the field of polyether modified silicone oil ternary copolymerization fabric finishing agent and polyester, and can solve the problems of poor fabric hand feeling, unsatisfactory repairability and hydrophilicity. and unsatisfactory durability, etc., to achieve the effect of high stability
- Summary
- Abstract
- Description
- Claims
- Application Information
AI Technical Summary
Problems solved by technology
Method used
Image
Examples
Embodiment 1
[0015] Allyl polyether uses the azeotrope of toluene and water to remove moisture and the silicone oil is dried with anhydrous magnesium sulfate, then add 720 grams of allyl polyether as the reaction raw material in a 2L reactor, with a hydrogen content of 0.10%-0.20% 33.6 grams of hydrogen-containing silicone oil, 264 grams of solvent toluene, and 150 ppm of isopropanol solution of chloroplatinic acid as a catalyst were heated to 120° C. under a nitrogen atmosphere, stirred evenly, and kept for 4 hours for reaction. Toluene and low boilers were distilled off at a vacuum of 0.09 Ma to obtain a transparent viscous liquid which was polyether modified silicone oil.
[0016] Add 144 grams of dimethyl terephthalate into a 2L reaction kettle, raise the temperature to 150°C, and after the dimethyl phthalate is completely dissolved, add 320 grams of ethylene glycol, and add a transesterification catalyst of manganese acetate and di 1 gram of compound of antimony is heated up to 190 DE...
Embodiment 2
[0018] Allyl polyether uses the azeotrope of toluene and water to remove moisture and the silicone oil is dried with anhydrous magnesium sulfate, then add 720 grams of allyl polyether as the reaction raw material in a 2L reactor, with a hydrogen content of 0.10%-0.20% 33.6 grams of hydrogen-containing silicone oil, 264 grams of solvent toluene, and 150 ppm of catalyst chloroplatinic acid isopropanol solution were heated to 140° C. under nitrogen atmosphere, stirred evenly, and kept for 2.5 hours for reaction. Toluene and low boilers were distilled off at a vacuum of 0.09 Ma to obtain a transparent viscous liquid which was polyether modified silicone oil.
[0019] Add 144 grams of dimethyl terephthalate into a 2L reaction kettle, raise the temperature to 140°C, and after the dimethyl phthalate is completely dissolved, add 320 grams of ethylene glycol, and add manganese acetate and di 1 gram of compound of antimony is heated up to 200 ℃ with the speed of 1 ℃ / min, carries out tra...
Embodiment 3
[0021] Allyl polyether uses the azeotrope of toluene and water to remove moisture and the silicone oil is dried with anhydrous magnesium sulfate, then add 720 grams of allyl polyether as the reaction raw material in a 2L reactor, with a hydrogen content of 0.10%-0.20% 33.6 grams of hydrogen-containing silicone oil, 264 grams of toluene as a solvent, and 150 ppm of isopropanol solution of chloroplatinic acid as a catalyst were heated to 130° C. under a nitrogen atmosphere, stirred evenly, and kept for 3 hours for reaction. Toluene and low boilers were distilled off at a vacuum of 0.09 Ma to obtain a transparent viscous liquid which was polyether modified silicone oil.
[0022] Add 144 grams of dimethyl terephthalate into a 2L reactor, heat up to 160°C, and after the dimethyl phthalate is completely dissolved, add 320 grams of ethylene glycol, and add manganese acetate and di 1 gram of compound of antimony is heated up to 180 ℃ with the speed of 1 ℃ / min, carries out transesterif...
PUM
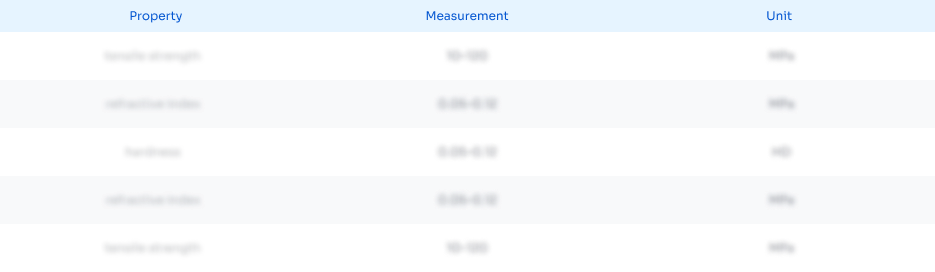
Abstract
Description
Claims
Application Information

- Generate Ideas
- Intellectual Property
- Life Sciences
- Materials
- Tech Scout
- Unparalleled Data Quality
- Higher Quality Content
- 60% Fewer Hallucinations
Browse by: Latest US Patents, China's latest patents, Technical Efficacy Thesaurus, Application Domain, Technology Topic, Popular Technical Reports.
© 2025 PatSnap. All rights reserved.Legal|Privacy policy|Modern Slavery Act Transparency Statement|Sitemap|About US| Contact US: help@patsnap.com