Supporting method of motion platform of machine tool
A technology of motion platform and support method, which is applied in the direction of metal processing machinery parts, measuring/indicating equipment, drilling/drilling equipment, etc., and can solve the problems that affect the life of guide rail sliders, long suspension sections, unevenness, etc. that affect the motion performance
- Summary
- Abstract
- Description
- Claims
- Application Information
AI Technical Summary
Problems solved by technology
Method used
Image
Examples
Embodiment Construction
[0023] In order to further illustrate the principle and structure of the present invention, preferred embodiments of the present invention will now be described in detail with reference to the accompanying drawings.
[0024] The supporting method of the motion platform of the machine tool of the present invention is: apply the vibration analysis theory to carry out the position layout and rigidity selection of the air-floating guide rail support of the motion platform of the machine tool, use the vibration test means to carry out the modal analysis and the work deformation analysis of the motion platform, and aim at the working process In order to solve the deformation problem of the motion platform, the position and stiffness of the air bearing guide rail support are improved by using the modal modification method, so as to realize the adjustment of the dynamic characteristics of the motion platform.
[0025] see figure 2 As shown, the supporting method of the machine tool m...
PUM
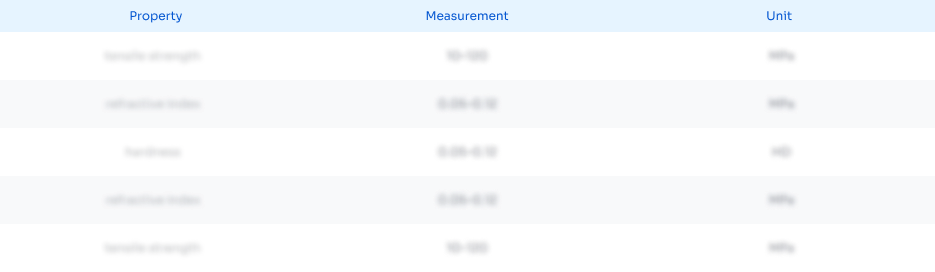
Abstract
Description
Claims
Application Information

- R&D Engineer
- R&D Manager
- IP Professional
- Industry Leading Data Capabilities
- Powerful AI technology
- Patent DNA Extraction
Browse by: Latest US Patents, China's latest patents, Technical Efficacy Thesaurus, Application Domain, Technology Topic, Popular Technical Reports.
© 2024 PatSnap. All rights reserved.Legal|Privacy policy|Modern Slavery Act Transparency Statement|Sitemap|About US| Contact US: help@patsnap.com