Fused direct spinning hyperfine denier polyurethane fibre device in single static agitated reactor
A reaction kettle, ultra-fine denier technology, applied in the field of spandex fiber production, to achieve the effects of small bending stiffness, strong cleaning function, and high water absorption
- Summary
- Abstract
- Description
- Claims
- Application Information
AI Technical Summary
Problems solved by technology
Method used
Image
Examples
Embodiment 1
[0010] 1. Take 75 kg of polyester polyol, 20 kg of isocyanate, and 5 kg of butanediol;
[0011] 2. Negative pressure feeding, evacuate to negative 0.8MPa pressure, add polyester polyol raw material into the first purification tank through the first feeding valve set on the first purification tank, temperature 103-105 ℃, heat for 45 minutes Purify; the raw material butanediol is added into the second purification tank through the second feeding valve arranged on the second purification tank, the temperature is 106-108 ° C, and it is purified by heating for 45 minutes; the isocyanate is purified through the The third feeding valve is added to the third purification tank, the temperature is 110-112 ° C, and the heating is carried out for 50-55 minutes for purification;
[0012] 3. Add 0.8MPa nitrogen pressure, pass the raw material in the first purification tank through the first metering delivery pump, the raw material in the second purification tank through the second met...
Embodiment 2
[0019] 1. Take 70 kg of polyester polyol, 25 kg of isocyanate, and 5 kg of butanediol;
[0020] 2. Negative pressure feeding, vacuumize to negative 0.8MPa pressure, feed polyester polyol raw material into the first purification tank through the first feeding valve installed on the first purification tank, temperature 103-105 °C, heat 41- Purify in 45 minutes; the raw material butanediol is added into the second purification tank through the second feeding valve arranged on the second purification tank, the temperature is 106-108 ° C, and the purification is carried out by heating for 45-54 minutes; the isocyanate is purified by setting in the third The third feeding valve on the purification tank is fed into the third purification tank at a temperature of 110-112°C and heated for 50-55 minutes for purification;
[0021] 3. Add 0.8MPa nitrogen pressure, pass the raw material in the first purification tank through the first metering delivery pump, the raw material in the s...
PUM
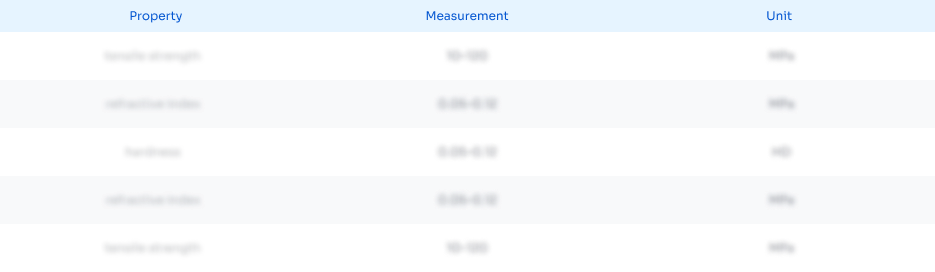
Abstract
Description
Claims
Application Information

- R&D Engineer
- R&D Manager
- IP Professional
- Industry Leading Data Capabilities
- Powerful AI technology
- Patent DNA Extraction
Browse by: Latest US Patents, China's latest patents, Technical Efficacy Thesaurus, Application Domain, Technology Topic, Popular Technical Reports.
© 2024 PatSnap. All rights reserved.Legal|Privacy policy|Modern Slavery Act Transparency Statement|Sitemap|About US| Contact US: help@patsnap.com