Method for preparing novel flame-retardant flexible polyurethane foam and product thereof
A technology of soft polyurethane and foam plastics, which is applied in the field of flame-retardant polyurethane foam plastics, can solve the problems of high price, limited application of soft polyurethane foam, and further improvement of flame-retardant effect, and achieves low production cost, easy industrial implementation, Inexpensive effect
- Summary
- Abstract
- Description
- Claims
- Application Information
AI Technical Summary
Problems solved by technology
Method used
Examples
Embodiment 1
[0021] (1) Weigh 100g of polyether polyol, 100g of isocyanate, 1g of foam stabilizer, 3g of blowing agent, 0.5g of tin catalyst, 0.5g of triethylenediamine as gel catalyst, 5g of flame retardant melamine, and attapulgite 5g. Using a one-step foaming process, sequentially add polyether polyol, foam stabilizer, catalyst, water and flame retardant into the beaker, and stir it evenly under high-speed electric stirring to obtain a viscous mixture.
[0022] (2) While stirring, quickly add the isocyanate into the viscous polyether polyol mixture while stirring rapidly. When the reactant starts to take on a milky white color, it is poured into pre-prepared molds. After the foaming is complete and solidified, put the mold filled with the foamed plastic into an oven, mature it at 40°C for 2 hours, and finally take out the mold and demould to obtain a flame-retardant flexible polyurethane foamed plastic product.
Embodiment 2
[0024] (1) Weigh 100g of polyether polyol, 100g of isocyanate, 1g of foam stabilizer, 4g of blowing agent, 0.5g of tin catalyst, 0.5g of triethylenediamine as gel catalyst, 10g of flame retardant melamine, and attapulgite 5g. Using a one-step foaming process, sequentially add polyether polyol, foam stabilizer, catalyst, water and flame retardant into the beaker, and stir it evenly under high-speed electric stirring to obtain a viscous mixture.
[0025] (2) While stirring, quickly add the isocyanate into the viscous polyether polyol mixture while stirring rapidly. When the reactant starts to take on a milky white color, it is poured into pre-prepared molds. After the foaming is complete and solidified, put the mold filled with foamed plastic into an oven, and mature it at 60° C. for 2 hours, and finally take out the mold and demould to obtain a flame-retardant flexible polyurethane foamed plastic product.
Embodiment 3
[0027] (1) Weigh 100g of polyether polyol, 100g of isocyanate, 2g of foam stabilizer, 4g of blowing agent, 0.5g of tin catalyst, 0.5g of triethylenediamine as gel catalyst, 10g of flame retardant melamine, and attapulgite 10g. Using a one-step foaming process, sequentially add polyether polyol, foam stabilizer, catalyst, water and flame retardant into the beaker, and stir it evenly under high-speed electric stirring to obtain a viscous mixture.
[0028] (2) While stirring, quickly add the isocyanate into the viscous polyether polyol mixture while stirring rapidly. When the reactant starts to take on a milky white color, it is poured into pre-prepared molds. After the foaming is complete and solidified, put the mold filled with the foamed plastic into an oven, mature it at 50° C. for 3 hours, and finally take out the mold and demould to obtain a flame-retardant flexible polyurethane foamed plastic product.
PUM
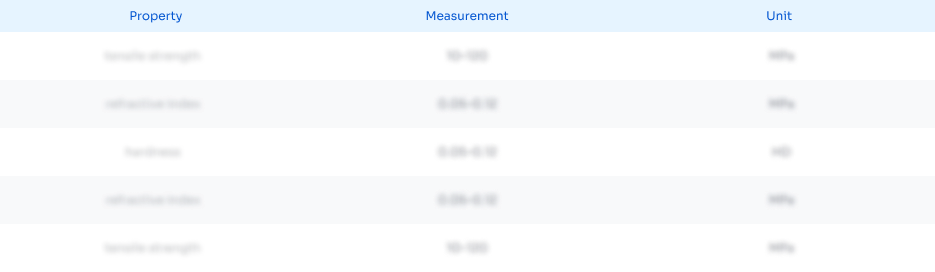
Abstract
Description
Claims
Application Information

- Generate Ideas
- Intellectual Property
- Life Sciences
- Materials
- Tech Scout
- Unparalleled Data Quality
- Higher Quality Content
- 60% Fewer Hallucinations
Browse by: Latest US Patents, China's latest patents, Technical Efficacy Thesaurus, Application Domain, Technology Topic, Popular Technical Reports.
© 2025 PatSnap. All rights reserved.Legal|Privacy policy|Modern Slavery Act Transparency Statement|Sitemap|About US| Contact US: help@patsnap.com