Downward and butt welding process for high strength steel for ship structure
A technology for structural steel and welding technology, applied in welding equipment, manufacturing tools, arc welding equipment, etc., can solve the problems of immature application and small proportion, and achieve the effect of saving raw materials, reducing production costs, and improving labor efficiency
- Summary
- Abstract
- Description
- Claims
- Application Information
AI Technical Summary
Problems solved by technology
Method used
Image
Examples
Embodiment 1
[0050] Using submerged arc automatic welding:
[0051] 1. The welding materials are as follows: welding wire H08Mn2EΦ5mm, flux CHF101
[0052] 2. Welding sequence and groove size such as figure 2 shown in figure 1 The double V-shaped groove on the foundation has a front fusion width of 60-62mm, a back fusion width of 50-52mm, a penetration depth of 100mm, and a residual height of 0-2mm; this type of groove can save more welding materials, electric energy and It is easy to process, can effectively reduce welding deformation, and has good weldability.
[0053] 3. The welding specification parameters are shown in the following table 1:
[0054] Table 1 Submerged arc automatic welding
[0055]
PUM
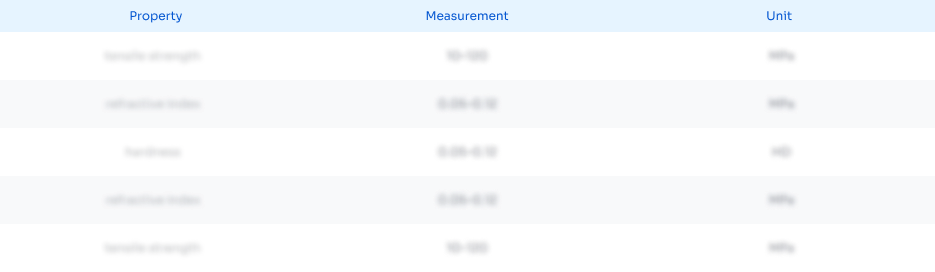
Abstract
Description
Claims
Application Information

- R&D
- Intellectual Property
- Life Sciences
- Materials
- Tech Scout
- Unparalleled Data Quality
- Higher Quality Content
- 60% Fewer Hallucinations
Browse by: Latest US Patents, China's latest patents, Technical Efficacy Thesaurus, Application Domain, Technology Topic, Popular Technical Reports.
© 2025 PatSnap. All rights reserved.Legal|Privacy policy|Modern Slavery Act Transparency Statement|Sitemap|About US| Contact US: help@patsnap.com