High-strength wear-resistant steel plate and preparation method thereof
A wear-resistant steel plate and high-strength technology, which is applied to the preparation of high-strength wear-resistant steel plates by an on-line quenching process, the heat treatment of the wear-resistant steel, the high-strength wear-resistant steel plates and their preparation fields, can solve the problems of high cost, poor plasticity, residual internal stress, etc.
- Summary
- Abstract
- Description
- Claims
- Application Information
AI Technical Summary
Problems solved by technology
Method used
Image
Examples
Embodiment 1
[0028] A method for preparing a high-strength wear-resistant steel plate by an on-line quenching process, wherein the chemical composition mass percentage content of the steel is: C is 0.18%, Si is 0.35%, Mn is 1.30%, Als is 0.041%, Cr is 0.65%, Ni 0.20% for Mo, 0.25% for Mo, 0.015% for Ti, 0.0020% for B, 0.013% for P, 0.080% for S, and the rest is Fe and unavoidable inclusions.
[0029] (1) In the heating process, while ensuring a certain austenite grain size of the billet matrix, the microalloying elements are fully dissolved, the heating temperature is 1200 ° C, and the soaking time is 80 minutes;
[0030](2) In the conventional rolling process, the rough rolling start temperature is 1170°C, the rough rolling finish rolling temperature is 1050°C, and the pass reduction rate is 15% to 28%; after the rough rolling is finished, the warm finish rolling is not carried out directly Start rolling, the starting rolling temperature is 992°C, the finishing rolling temperature is 935°...
Embodiment 2
[0033] A method for preparing a high-strength wear-resistant steel plate by an on-line quenching process, wherein the chemical composition mass percentage content of the steel is: C is 0.17%, Si is 0.41%, Mn is 1.32%, Als is 0.038%, Cr is 0.56%, Ni 0.26% for Mo, 0.30% for Mo, 0.015% for Ti, 0.0020% for B, 0.013% for P, 0.070% for S, and the rest is Fe and unavoidable inclusions.
[0034] (1) In the heating process, while ensuring a certain austenite grain size of the billet matrix, the microalloying elements are fully dissolved, the heating temperature is 1210 ° C, and the soaking time is 71 minutes;
[0035] (2) In the conventional rolling process, the rough rolling start temperature is 1800°C, the rough rolling finish temperature is 1061°C, and the pass reduction rate is 15% to 28%; after the rough rolling is finished, the warm finish rolling is not carried out directly Start rolling, the starting rolling temperature is 1009°C, the finish rolling and finishing rolling temper...
Embodiment 3
[0039] A method for preparing a high-strength wear-resistant steel plate by an on-line quenching process, wherein the chemical composition mass percentage content of the steel is: C is 0.19%, Si is 0.35%, Mn is 1.30%, Als is 0.041%, Cr is 0.60%, Ni 0.20% for Mo, 0.25% for Mo, 0.015% for Ti, 0.0020% for B, 0.014% for P, 0.060% for S, and the rest is Fe and unavoidable inclusions.
[0040] (1) In the heating process, while ensuring a certain austenite grain size of the billet matrix, the microalloying elements are fully dissolved, the heating temperature is 1230 ° C, and the soaking time is 65 minutes;
[0041] (2) In the conventional rolling process, the rough rolling start temperature is 1185°C, the rough rolling finish temperature is 1080°C, and the pass reduction rate is 15% to 28%; after the rough rolling is finished, the warm finish rolling is not carried out directly Start rolling, the starting rolling temperature is 1060°C, the finishing rolling temperature is 958°C, the...
PUM
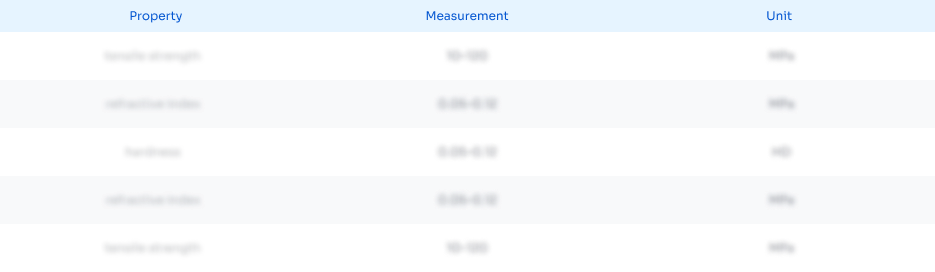
Abstract
Description
Claims
Application Information

- R&D Engineer
- R&D Manager
- IP Professional
- Industry Leading Data Capabilities
- Powerful AI technology
- Patent DNA Extraction
Browse by: Latest US Patents, China's latest patents, Technical Efficacy Thesaurus, Application Domain, Technology Topic, Popular Technical Reports.
© 2024 PatSnap. All rights reserved.Legal|Privacy policy|Modern Slavery Act Transparency Statement|Sitemap|About US| Contact US: help@patsnap.com